ЕЩЕ ДВА ИЗОБРЕТЕНИЯ
ЕЩЕ ДВА ИЗОБРЕТЕНИЯ
Второе изобретение родилось значительно легче, чем первое. Может быть, это произошло потому, что за него я взялся не один. Моим соавтором стал товарищ по работе, токарь-резьбовик Иван Петрович Иванов.
Земляк-ленинградец, переехавший в Москву, он давно занимался нарезкой резьбы на мелких метчиках (диаметром от 2 до 5 мм). Таких метчиков на нашем заводе требовалось тысячи, а, несмотря на высокую квалификацию и отличную ленинградскую выучку, Иван Петрович явно не справлялся с заданием. Он работал напряженно, не отходя от станка ни на минуту, но больше сотни метчиков в смену дать не мог. Что поделаешь — резьба есть резьба, на ней не разбежишься!
— Послушай, изобретатель, хоть бы ты придумал что-нибудь, новый инструмент, что ли, — несколько раз говорил Иван Петрович. — Видишь, совсем замаялся я со своими метчиками!
Сначала я отшучивался, а однажды как-то сказал Ивану Петровичу:
— Давай-ка вместе подумаем, что тут можно сделать. Сперва решим, за счет чего можно увеличить выпуск мелких метчиков.
Мы внимательно разобрались в специфике изготовления метчиков и, не помышляя еще об изобретении, пришли к выводу, что технологию надо коренным образом менять. Были возможны три пути:
1 — вместо нарезания применить накатывание резьбы;
2 — получать резьбу на резьбошлифовальном станке, обрабатывая заготовки в каленом виде;
3 — усовершенствовать резьбовую гребенку — инструмент, которым нарезают резьбу на мелких метчиках.
Все это я выложил Ивану Петровичу, и он тут же обстоятельно возразил мне:
— Что ты толкуешь про накатывание резьбы на метчиках? — возмущенно сказал он. — Разве ты не видел кучи метчиков завода «Фрезер», что свалены в угол в инструментальной кладовой? Ведь это все метчики с накатанной резьбой. Никто их не берет, они даже латунь не режут. Нет, нам это не подойдет. Мы работаем «не с пуда», да и материалы у нас обрабатываются крепкие, для них нужны хорошие метчики.
Действительно, накатанные метчики, выпускавшиеся тогда заводом «Фрезер», имели у вершины резьбы сильно сжатую и нарушенную структуру металла, отчего после термообработки резьба на них выкрашивалась при первом же прикосновении даже к цветным металлам.
Ну, а что ты скажешь относительно резьбошлифовки? — спросил я.
Тоже плохо, — подумав, ответил Иван Петрович, — у мелкой резьбы вершина острая, почти как бритва, и резьбошлифовальный круг непременно будет ее отжигать. Значит, метчики опять не будут резать.
А если шлифовать на малых скоростях и с малой подачей? — возразил я. — Ведь тогда можно получить неотожженную вершину у резьбы!
Можно-то можно, — сказал Иван Петрович, — но это будет еще медленнее, чем я сейчас нарезаю гребенкой!
Что же нам тогда остается? Остается одно — усовершенствовать инструмент, которым я нарезаю метчики, — заключил беседу Иван Петрович.
Ну вот что, — предложил я, — завтра мы с тобой пойдем в Патентную библиотеку и посмотрим, что создано в мире по этому виду инструмента. Только сперва ты мне покажи, что у тебя самого есть по этой части?
Вдвоем мы довольно быстро выяснили следующее. Резьбу на мелких метчиках можно нарезать дисковым резцом, доведенным до высокого класса чистоты и имеющим почти теоретическое острие у вершины. Но нарезать дисковой гребенкой с несколькими режущими зубьями более производительно, так как три или четыре острия гребенки не так быстро «сядут» при нарезке, как одно острие дискового резца.
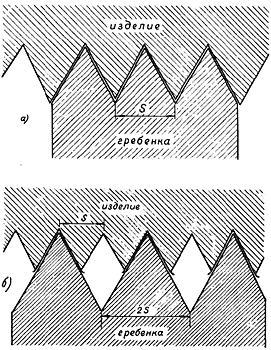
Схема нарезания резьбы гребенкой:
а — одинакового с изделием шага;
б — с удвоенным шагом.
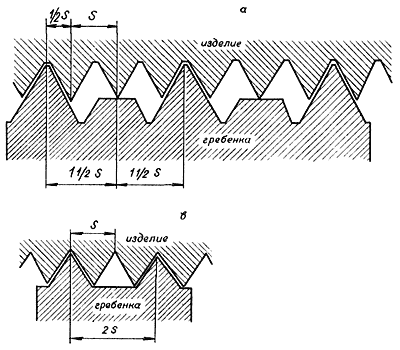
Схема работы и профиль гребенки для нарезания резьбы метчиков:
а — по довоенному немецкому патенту;
б — по авторскому свидетельству № 142118, выданному Б.Ф. Данилову и И.П. Иванову.
Однако тут возникают неприятности. Когда после нескольких проходов работа подходит к завершению, резьба метчика срывается по наружному диаметру. Происходит это потому, что отходящему металлу некуда деваться, и стружка срывает резьбу у почти готового метчика.
Иван Петрович предложил нарезать метчики гребенкой, которая имела бы шаг в 2 раза больший, чем резьба на метчике, т.е. резьбу с шагом 0,5 мм резать гребенкой с шагом 1 мм. В этом случае вершина резьбы не касается гребенки и срыва наружного диаметра резьбы не произойдет. Но тут возникает новая неприятность: при нарезке такой гребенкой наружный диаметр резьбы поднимается, «выжимается» зубьями гребенки и становится выше допуска. Кроме того, на резьбе появляются заусенцы, хорошо видимые под микроскопом.
Чтобы сделать наружный диаметр метчика правильным, приходилось его на ходу спиливать напильником или ставить другой резец и протачивать резьбу по верху. Появлялась дополнительная операция, кроме того, после напильника и резца образовывались новые заусенцы, теперь уже с двух сторон резьбы. Они тоже были хорошо видны под микроскопом. Вот почему Иван Петрович, при всем его трудолюбии, никак не мог нарезать более 100 метчиков в день.
В Патентной библиотеке из множества наших и зарубежных патентов мы выбрали только один. Это был еще довоенный германский патент. Там была изображена резьбовая гребенка, которая, казалось, сразу отметала все наши затруднения.
— Дотошный народ эти немцы, — заметил Иван Петрович, — еще тридцать лет назад решили наш вопрос, и, кажется, неплохо.
Но я был далеко не в восторге от этого инструмента. Действительно, при нарезании такой гребенкой срыва наружного диаметра резьбы не произойдет, не будет и заусенцев, потому что средний неполный зуб гребенки снимет, при малой подаче, возникшие заусенцы. Но было два «но»!
При нарезке ручных и машинных метчиков такой гребенкой обязательно надо оставлять недорезанными по крайней мере три витка, а это не допускается по нормали. Гребенка годилась только для нарезки резьбы «на проход».
Чтобы получить нужный профиль на гребенке, надо сделать ее шаг в два раза больше, чем на метчике. Но, чтобы снять до половины каждый второй виток гребенки, она должна быть двухзаходная. Как специалист по резьбе, я представлял, насколько сложно будет выполнить такой профиль в металле. Даже не сразу сообразил, как бы я составил рабочий чертеж этой немецкой гребенки.
Мы просидели в Патентной библиотеке весь вечер и ушли несколько смущенные. Толчок нашим мыслям был дан, но до решения, казалось, еще далеко. Однако оно пришло неожиданно быстро — на другой же день.
Иван Петрович с утра подошел к моему станку и стал что-то рисовать на листке из блокнота. Сперва я не очень внимательно его слушал, но потом как-то вдруг до меня дошли его рассуждения. К нарисованной им схеме я подрисовал буквально только одну линию — и сразу получился рабочий чертеж новой гребенки. Как и немецкая, она полностью решала все вопросы и, кроме того, не имела ни одного «но». Она была проста, мы могли сделать ее хоть сейчас!
Гребенку надо сделать с удвоенным шагом против шага резьбы метчика, но внутренний ее диаметр не резать до острия, как обычно, а сделать внутри мерную площадку, равную шагу резьбы метчика. Такая гребенка никогда не сорвет резьбу по наружному диаметру, так как во время процесса нарезания всегда будет пустота между нарезаемой резьбой и гребенкой, а при последней стружке, дающей окончательный размер метчику, мерная площадка гребенки мягко снимет заусенец, возникший по наружному диаметру резьбы.
Мы были несказанно рады, что нашли такое простое решение задачи. Даже без испытания мы были убеждены, что она будет отлично работать и даст резьбовикам большие преимущества. Это был тот редкий случай, когда эффективность новшества ясна на бумаге, до изготовления в металле. Тем не менее мы проявили осторожность и не подавали в бриз предложения, пока не изготовили первую гребенку и пока Иван Петрович не начал ею работать.
Результат получился неожиданный. Раньше мастер все время просил Иванова остаться поработать сверхурочно, «поднажать», так как метчиков заводу надо было очень много. Через полтора месяца после изготовления новой гребенки мастер пришел с другой претензией:
— Послушай, Иван Петрович, мне нечего тебе дать на нарезку! Заготовщицы не поспевают за тобой. Когда ты успел нарезать все заготовки? Сверхурочно давно не оставался, в выходные дни не работаешь, а метчики все нарезал! Ты колдун, что ли?
Конечно, мастер не мог заметить, что на станке у Иванова стоит совсем не та гребенка, какая стояла десятки лет у всех резьбовиков. Внешне гребенки ничем не отличались, разницу можно было заметить только при рассмотрении в лупу или под микроскопом. Ведь резьбу-то он резал мелкую — с шагом от 0,4 до 0,8 мм! Теперь Иван Петрович работал на таких режимах: скорость — 400 оборотов в минуту, нарезка — за три прохода, четвертый — зачистной. На один метчик со всеми зажимами и отжимами заготовки уходило меньше минуты! Качество резьбы получалось отменное, никаких дополнительных операций не требовалось. Вместо 100 штук за смену Иванов теперь легко нарезал 500 метчиков и значительно лучшего качества.
Вскоре у новой гребенки были обнаружены еще некоторые преимущества. При нарезании такой гребенкой средний диаметр резьбы метчика всегда соответствует ее наружному диаметру, поэтому отпадает необходимость проверять метчики по среднему диаметру. Это происходит потому, что площадка гребенки рассчитана так, что она всегда дает нужную высоту профиля резьбы. Теперь достаточно простым микрометром измерить наружный диаметр метчика после нарезки, и если он окажется правильным, то и средний диаметр тоже будет в допуске.
Это очень важное преимущество. Ведь для того чтобы точно измерить средний диаметр резьбы метчика, приходится подчас потратить времени больше, чем на его нарезку. Наша гребенка стала быстро «входить в моду». Оказалось, что с ее помощью очень удобно нарезать резьбу не только на инструменте, но и на деталях. Отсутствие заусенцев и легкость замера резьбы по наружному диаметру делали этот инструмент очень удобным для использования в механических цехах на нарезке точной резьбы.
Забегая вперед, скажу, что позднее Центральное статистическое управление СССР прислало нам извещение о том, что наша гребенка внедрена на многих заводах страны. Но тогда мы и не помышляли о широком применении нашего скромного новшества. Однако я решил показать гребенку своему другу и наставнику в изобретательских делах — Евгению Александровичу Майкапару.
Он долго вертел гребенку перед глазами, рассматривая через лупу.
— Ничего не понял, Борис Федорович! — сказал он наконец. — Тут есть какая-нибудь специфика инструментального дела? В чем тут соль, расскажите.
Я рассказал и про германский патент, и про наши искания, и про результаты, которые дает гребенка. Евгений Александрович внимательно выслушал и сказал:
— Ну что же, Борис Федорович, во всем этом есть изюминка. Попробуйте подать заявку в Институт патентной экспертизы, я желаю вам обоим успеха!
Без совета Майкапара мы, вероятно, не рискнули бы подать заявку на столь, как нам казалось, скромное новшество.
Однако Майкапар оказался прав: на гребенку нам выдали авторское свидетельство № 142118. Вместе с другими моими инструментами наша гребенка в 1963 г. экспонировалась на ВДНХ в павильоне «Машиностроение». За нее и за другие новые инструменты я получил Большую серебряную медаль, Иван Петрович — бронзовую медаль.
* * *
Третье изобретение рождалось долго и трудно. Работа над ним началась, если не ошибаюсь, еще в 1962 г., когда я даже не предполагал, что эта случайно начатая работа приведет меня к изобретению.
Как-то я разговорился с главным резьбошлифовщиком нашего завода Михаилом Власьевичем Давыдовым, большим специалистом своего дела. У нас были свободными несколько минут, и мы наблюдали за работой доводчиков гладких калибров. Высококвалифицированные токари-доводчики работали, как автоматы. Каждый из них доводил за смену 100 и более гладких калибров, а заводу постоянно не хватало их! Дело в том, что калибры 2-го и 1-го классов точности, о которых идет речь, имеют весьма малый допуск на изготовление и на износ: всего 2-4 микрона.
Естественно, что калибры, которыми измеряют точные отверстия, при серийном выпуске деталей быстро изнашиваются, и их списывают в брак контрольные пункты. Вот почему так напряженно работают наши доводчики, вот почему завод «Калибр» ежегодно выпускает полтора миллиона калибров, а их все равно не хватает. А ведь калибры делаются из дорогой легированной стали, их доводка требует большого мастерства, поэтому они так дороги.
- Хорошо бы сделать такой калибр, который не изнашивается, — сказал Давыдов.
— Да, неплохо бы, — ответил я. — Давай сделаем гладкие калибры из твердого сплава, а?
Михаил Власьевич задумался.
— Что же, попробовать можно, — наконец сказал он.
В то время на заводах почти не было алмазных кругов, твердый сплав предоставлялся заводам только в виде прямоугольных пластинок для резцов. Так что для того времени наше решение было довольно смелым. Но кое-что о твердых сплавах мы, конечно, уже знали, в частности, были уже знакомы с пластификатом.
Еще будучи в Горьком, на автозаводе, мы с начальником цеха Романовым надолго задержались в лаборатории твердосплавных фасонных дисковых резцов. Здесь работали всего трое: прессовщица, токарь и спекальщик.
Они делали фасонные резцы для автоматов и револьверных станков. О преимуществах такого резца нам рассказывать было не нужно, каждому понятно, что такой резец обработает без переточки в сто раз больше деталей, чем стальной. Кроме того, работая твердосплавным резцом, можно раза в три повысить скорости резания. Резцы очень похожи на те, какие в начале рабочей карьеры я делал когда-то на заводе «Пневматика». Но я точил их из быстрорежущей стали, а здесь их делали из твердого сплава! Было от чего прийти в изумление и остаться в лаборатории на лишние полтора-два часа. Мы остались и все увидели.
Как все это делалось? Прессовщица насыпала в форму порошок и прессовала из него круглую толстую лепешку. Мы знали, что эта лепешка представляет собой рыхлую массу, которая может рассыпаться в руках; чтобы получить твердый сплав, ее надо немедленно спечь. Однако здесь делалось по-другому: лепешку осторожно опускали в кипящий парафин с примесью каучука, парафин проникал в мельчайшие поры, и после остывания получалась настолько прочная и плотная масса, что ее можно было зажать в патрон или посадить на оправку и обрабатывать резцами, как обычный легкий металл!
Это был пластификат твердого сплава. Автор его — советский ученый В.П. Ивенсен. При нас токарь поставил такую лепешку на станок, произвел на бумажке какие-то расчеты и стал вытачивать профиль фасонного резца. На этот раз профиль был простой, и токарь быстро передал сырой резец спекальщику, — специальная печь для спекания твердого сплава стояла тут же.
В современных лабораториях процесс спекания обычно длится 23 часа. Не знаю, сколько времени занимал этот процесс на Горьковском автозаводе, но нас пригласили зайти на другой день, если мы хотим видеть до конца процесс изготовления фасонного твердосплавного резца.
На другой день в нашем присутствии токарь вскрыл и заточил фасонный резец. После остановки заточного круга я посмотрел на его маркировку на торце. Это был алмазный круг американской фирмы «Нортон». Производство синтетических алмазов у нас тогда только зарождалось, и на наших заводах не было алмазного инструмента широкого профиля. Горьковский автозавод — самое передовое предприятие страны — получал алмазные круги из Соединенных Штатов Америки за очень большие деньги. Но твердосплавный фасонный инструмент давал такой большой эффект, что все затраты оправдывались. Необычайную эффективность инструмента из твердого сплава я понял еще тогда и до сих пор считаю выгодным для нашей промышленности перевести почти весь инструмент на твердый сплав.
Токарь поставил заточенный фасонный резец на станок, на какой-то невероятной скорости буквально «чиркнул» им по заготовке и показал нам готовую деталь, предложив проверить ее по шаблону. Шаблон лег на деталь, как влитый.
Мы поблагодарили за науку и вышли из лаборатории.
— Да, настоящий инструмент делают мои земляки, нам еще до этого далеко! — с некоторой завистью сказал Романов.
Я крепко запомнил, что такое пластификат твердого сплава и каковы его возможности.
Мы с Давыдовым рассуждали так. Пластификат у нас есть. Я выточу заготовку гладкого калибра с отверстием под оправку, потом нам спекут ее в Институте твердых сплавов (ВНИИТС). Затем мы посадим заготовку на оправку, и Михаил Власьевич прошлифует ее зеленым карборундовым кругом с припуском на доводку. Я доведу алмазной пылью калибр до размера и посажу его прессовой посадкой на шейку хвостовика. Потом хвостовик вставим в ручку — и калибр готов к работе.
Все было сделано, как задумано. Разумеется, мы работали вечерами, после смены. Старались делать все тайно по двум причинам: во-первых, мы не совсем были уверены в успехе, во-вторых, на нашем заводе, как я уже говорил, тогда было немало противников нового в технике.
Нам удалось сделать всего 30 гладких твердосплавных калибров. Они были приняты центральной измерительной лабораторией завода и переданы в механические цехи на участки массовых и серийных деталей. Это было в 1962 г. Забегая вперед, скажу, что и теперь эти калибры продолжают работать на участках самых интенсивных замеров и до сих пор на них не обнаруживается ни одного микрона износа. А ведь за это время изношены и списаны в утиль тысячи стальных калибров! Кроме крайне высокой износостойкости у наших калибров есть и другие преимущества.
Вскоре после изготовления первых гладких калибров из твердого сплава к нам пришел заведующий инструментальным хозяйством одного из цехов.
Можно сделать такой калибр, у которого проходная сторона в нижнем допуске, а непроходная сторона — в верхнем допуске?- спросил он у меня.
Теоретически это возможно, — ответил я, — но зачем это вам?
Как зачем! Для того чтобы спасти тысячи бракуемых сейчас деталей! Вы часто делаете гладкие калибры так: проходной калибр — в верхнем допуске, а непроходной — в нижнем. Допуск у вас, скажем, на калибр 30А — 4 микрона, а разница между проходным и непроходным калибрами — 14 микрон. Вот вы сделали непроходной калибр в нижнем допуске — у нас уже осталась всего одна сотка разницы! А вы сделайте нам наибольшую разницу!
— Но ведь если сделать вам проходной калибр в нижнем допуске, то после сотни замеров его вам забракуют на контрольном пункте, — возразил я, — он только чуть-чуть износится и уже пойдет в брак!
— А вы сделайте так, чтобы он не изнашивался, вы же теперь можете это сделать! — не унимался дотошный заведующий инструментальным хозяйством.
Конечно, теперь мы с Давыдовым могли сделать такие калибры из твердого сплава и сделали их. Тысячи деталей были спасены, новые детали стало делать легче, так как допуск на их изготовление мы практически увеличили на 6-8 микрон, не отступив при этом ни на йоту от ГОСТа.
Эти калибры образца 1962 г. до сих пор работают в механическом цехе и до сих пор не изношены, хотя для забракования проходной стороны достаточен износ в 1-2 микрона.
Доводчикам известны неприятные случаи, когда гладкий калибр застревает в измеряемом отверстии и его оттуда приходится выколачивать. Обычно при этом портится и деталь и калибр. Происходит это потому, что при частых промерах деталей обычный проходной калибр быстро изнашивается у начала и начинает входить в деталь, когда еще не готов размер.
Твердосплавный гладкий калибр всегда намного тверже любой стальной закаленной детали. Доведенный до 11-го или 12-го класса чистоты, он очень скользкий и никогда не застревает в детали. Кроме того, у него не бывает износа у начала, как у стального калибра, поэтому ввести его в неготовую деталь просто невозможно.
Доводчики механических цехов все это быстро усвоили и стали просить у нас гладкие твердосплавные калибры нужных им размеров.
Чтобы как-то узаконить наши калибры, я и Давыдов подали предложение в Бриз. Сделали это мы только спустя примерно год после начала эксплуатации первых твердосплавных калибров.
Центральная измерительная лаборатория завода, следящая за износом калибров во всех цехах, дала предварительное заключение о том, что стойкость новых калибров, по крайней мере, в 200 раз выше стойкости обычных, стальных.
Реакция на нашу заявку была самой неожиданной. К нам пришел уполномоченный бриза и заявил: «Ваше предложение отклонено, и скажите спасибо, что с вас не высчитывают деньги за сделанные вами первые партии калибров».
Мы раскрыли рты от изумления и дали возможность этому «бризу» уйти, не выслушав нашего мнения о его способностях.
Начальник отдела труда и зарплаты Власов объяснил нам все по-деловому:
— Вот смотрите, как у нас рассчитываются рационализаторские предложения, — показал он инструкцию. — Вот здесь пишется стоимость выпускаемого инструмента до предложения, а здесь — стоимость после предложения. Из большего вычитается меньшее и получается экономический эффект. Стоимость ваших калибров стала не меньше, а больше в 8 раз, поэтому не вам полагается вознаграждение, а с вас надо еще получить деньги за удорожание выпускаемого инструмента. Но мы решили вас не обижать, а просто отклонили предложение.
Все это Власов объяснил нам спокойно, как учитель объясняет ошибку школьникам. После этого случая Давыдов на некоторое время охладел ко всякой рационализации и временно перестал быть моим партнером в этой области.
Больше мы не сделали ни одного гладкого калибра из твердого сплава, и на заводе до сих пор работают только первые наши калибры образца 1962 г.! И опять приходится вспомнить Московский совет новаторов. Если бы тогда в Москве не было этой организации — кто знает, сколько бы лет прошло, прежде чем наши заводы получили бы необычайно стойкий и нужный всем инструмент?
На очередном заседании секции токарей гладкие твердосплавные калибры были приняты единогласно. Здесь были советские специалисты, твердо знающие, что выгодно и что невыгодно нашей промышленности. Рекомендация Совета новаторов была принята Мосгорсовнархозом, который обязал завод «Калибр» выпустить в 1963 г. первую тысячу комплектов твердосплавных гладких калибров.
Меня пригласили на «Калибр». Вместе с заводскими специалистами мы отработали технологический процесс изготовления новых калибров, и они были выпущены в срок, указанный в распоряжении совнархоза.
Поддержка товарищей из Совета новаторов и совнархоза вдохновила меня на новую, более серьезную работу в области твердосплавного инструмента — я «замахнулся» на резьбовые калибры-кольца из твердого сплава! Даже в 1969 г., просмотрев проспекты почти всех иностранных инструментальных фирм, я не нашел там резьбовых калибровых колец из твердого сплава. Известная швейцарская фирма «Кару», снабжающая мерительным инструментом заводы всех капиталистических стран, предлагала своим потребителям только гладкие твердосплавные калибры.
Бывая на иностранных промышленных выставках, каждое лето организуемых в «Сокольниках», я не раз спрашивал зарубежных специалистов о твердосплавных резьбовых калибрах, и всегда английские, французские, немецкие, швейцарские хозяева экспонатов на мой вопрос только вежливо разводили руками: «Не делаем; не выпускаем; можем предложить гладкие твердосплавные калибры!»
«А может быть, их так сложно сделать, что они не оправдают затраченные на них усилия? — думал я. — Ведь почему-то не делает таких колец ни одна инструментальная фирма!»
Да нет, не могут они быть невыгодными. Гладкие калибры в 200 раз более стойки, чем стальные, значит, и резьбовые будут иметь такую же невероятную долговечность. Ну, пусть они будут в 10 раз дороже, чем стальные резьбовые кольца такого же размера. Все равно они будут во много раз выгоднее, чем стальные!
Судьбу резьбовых твердосплавных колец решил один разговор с представителем очень солидной английской фирмы «Матрикс», выпускающей первоклассные станки и инструмент. Разговор шел через моего «личного» переводчика — сына Валерия. На вопрос: «Можно ли сделать твердосплавное калибровое кольцо?» — представитель фирмы ответил: «Теоретически возможно, но не стоит, так как это будет чересчур сложно и дорого!»
Как это ни странно, но именно тогда я про себя решил: «Будут дешевые русские твердосплавные резьбовые кольца!» Конечно, кое-какие мысли об этом бродили в голове и раньше, но теперь я взялся за это дело вплотную.
Очевидно, надо было делать прежде всего кольца наиболее ходовых размеров, которые больше всего и быстрее всего изнашиваются. А по опыту я знал, что изнашиваются больше всего кольца с метрической резьбой размером от 3?0,5 до 27?3. Значит, для пробы надо сделать кольца среднего размера, скажем, 14?1,5.
Метрическое резьбовое кольцо имеет двойной профиль: рабочий профиль с углом 60° и провал с углом 30°. Нарезать резьбу внутри кольца из пластификата специально заточенным твердосплавным резцом дело несложное. Но затем надо сразу решить три вопроса: как попасть в нитку вторым резцом с углом 30°, чтобы сделать провал и при этом не разрушить пластификат; как снять заходы резьбы с двух сторон кольца; как подсчитать такой шаг резьбы, который надо нарезать на сыром пластификате, чтобы после спекания получить точный шаг, скажем 1,5 мм.
При изготовлении стальных колец сперва нарезают резцом профиль с углом 60°, потом резцом с углом 30° попадают во впадину резьбы и прорезают провал. Прорезка провала — операция довольно щекотливая, поэтому для колец диаметром до 20 мм обычно делают метчики-провальники, которые, имея конус, постепенно попадают в нарезанный профиль с углом 60° и прорезают его. Кольца же диаметром больше 20 мм приходится прорезать резцом с углом 30°. Для этого надо «попасть в нитку», как говорят резьбовики, т. е. надо остановить станок и ввести острие резца с углом 30° во впадину резьбы. При этом почти обязательно резец легко касается уже нарезанного профиля. Для стальных колец такое касание не опасно. Пластификат же не терпит ни малейшего касания без вращения, он сразу разрушается: испортив несколько колец, я убедился в этом.
Попытка нарезать резьбу внутри кольца из пластификата метчиками оказалась еще более безнадежной. Несмотря на свою мягкость и хрупкость, пластификат твердого сплава, будучи составлен из весьма твердых компонентов, моментально «съедает» любой режущий инструмент, даже если этот инструмент сделан из спеченного твердого сплава. Пластификат хорошо обрабатывается твердосплавными резцами только при следующих условиях: резец должен быть из сплава марки Т15К6 или ВК.6М; должен быть заточен на алмазном круге до чистоты не ниже 11-го класса и иметь задний и передний углы по 10°. Резец должен быть острым, как бритва, и не иметь ни малейших зазубрин. Только тогда он будет стоять долго и хорошо резать пластификат.
Итак, моя попытка решить первый вопрос сорвалась. Со вторым вопросом дело обстояло не лучше. На стальных кольцах заходы резьбы снимают фрезой на токарном или фрезерном станке, для чего кольцо навинчивают на калибр-выработку. Резьбу, нарезанную в пластификате, навернуть на что-нибудь оказалось делом невозможным — кольцо сразу же разваливалось…
И наконец, третий вопрос — о шаге резьбы кольца из пластификата. Все размеры заготовки пластификата после спекания уменьшаются. На каждую партию пластификата завод-изготовитель дает паспорт, в котором указывается коэффициент усадки (К.У.), обычно он равняется 1,24-1,28. Это значит, что все линейные размеры будущего инструмента надо помножить на указанную величину (скажем, на 1,28) и выдержать эти размеры на сыром пластификате. Когда делали гладкие твердосплавные калибры, мы обращали внимание на диаметр заготовки, получающийся после спекания, но никогда не измеряли длину калибра. Тут коэффициент нас никогда не обманывал.
Каково же было мое разочарование, когда с большим трудом нарезанные без провала и без захода кольца вернулись ко мне после спекания с шагом не 1,5, а 1,56! Раз шаг резьбы был неверным, то доводить такое кольцо было просто бессмысленно.
Думая, что это случайность, повторил опыт. Результат был тот же. В общем, прошло два месяца, а все три вопроса остались неразрешенными. Советоваться было не с кем: ведь никто и нигде еще не делал резьбовых калибровых колец из твердого сплава. Как же быть? Последовать известной украинской поговорке: «Не трать, куме, силы, спускайся на дно»? Или продолжать поиск?
Иногда мелькала мысль: «А на кой черт мне они приснились, эти кольца? Не выходит, ну и пес с ними! У меня хватает достаточно сложной и интересной работы на каждый день. Зачем мне ломать голову над неразрешимой проблемой?»
И все же я не сдался, чувствовал, что не могу отступить. Видимо, изобретательство постепенно становилось моей второй профессией.
Поиск продолжался. Работу приходилось вести урывками, результаты экспериментов получались медленно, так как один только процесс спекания на опытном заводе твердых сплавов, с которым у нас был договор, длился три недели.
Работая вечерами в цехе, а дома за полночь засиживаясь за столом, через полгода я все-таки решил все три вопроса. И, как это часто бывает, решения оказались на редкость простыми, доступными пониманию даже неискушенного в инструментальном деле человека. Итак, задача первая — нарезка профиля резьбы с углом 60° и провала в 30° в сыром пластификате. Ответ — не надо вообще нарезать профиль с углом 60°, нарезка метрической резьбы ведется одним резцом с углом 30°.
Внутренний диаметр кольца растачивается с припуском на доводку после спекания и с учетом коэффициента усадки. Так же математически рассчитывается глубина, на которую надо прорезать резьбу резцом с углом 30°, чтобы после спекания получить наибольший диаметр кольца заведомо выше, чем наименование (размер) резьбы.
После спекания доводка резьбы производится обычным чугунным притиром с крупной алмазной пастой.
Для доводки десяти колец нужны четыре резьбовых притира. Первый притир быстро снимает острые углы профиля и оставляет на нем ленточку с углом 60°. Второй и третий притиры расширяют эту ленточку до нормальных размеров метрической резьбы. Доводка идет быстро, так как острие притира никогда не коснется твердого сплава, а будет всегда в пустоте. Ведь провал в 30° у нас прорезан выше возможного теоретического острия угла 60°. Применение крупной зернистой алмазной пасты очень сильно содействует быстрому образованию нужного профиля.
Четвертый притир, шаржированный мелкой алмазной пастой АП-10, доводит резьбу окончательно по контрольным резьбовым калибрам. Процесс доводки твердосплавного резьбового калибрового кольца ничем не отличается от доводки обычного стального кольца.
Так была решена первая проблема.
Вторая проблема — снятие заходов резьбы с двух сторон. Эта обязательная операция предусмотрена ГОСТом для всех видов калибров (пробок и колец), и от нее никуда не уйти. Для снятия заходов на сыром пластификате пришлось вспомнить способ нарезания внутренней резьбы на резьбовых прессформах. Все токари-инструментальщики знают, что резьба прессформ должна иметь чистый сбег и заход и начинаться с полного профиля. А как делается заход резьбы у прессформы, я знал хорошо.
Таким образом, и решение второго вопроса оказалось не очень-то замысловатым.
С третьим вопросом пришлось повозиться подольше. Шаг резьбы… В чем дело, почему коэффициент усадки, указанный в паспорте, оказывается непригодным для расчета шага на сыром пластификате? И почему на это никто не обратил внимания и не сообщил заводу-изготовителю?
Ответ напрашивался сам собой: потому, что еще никто не делал резьбовых калибровых колец из твердого сплава, никому не было дела до этого шага! А мне этот шаг резьбы был очень нужен. Приходилось думать. Не сразу пришло решение. Вот какой я сделал наконец вывод.
Коэффициент усадки зависит от плотности прессования порошка твердого сплава. Обычно заготовка (цилиндрик) твердого сплава прессуется в форме давлением на торец. Никому не придет в голову прессовать заготовку давлением на круглую поверхность цилиндра. Естественно, что по направлению к дну цилиндра плотность прессования будет больше, чем в стороны, к стенкам цилиндра-заготовки.
До сих пор изготовителя интересовали только К.У. относительно диаметра заготовки, а меня интересовал К. У. не в отношении диаметра заготовки, а в отношении длины заготовки. Шаг резьбы ведь измеряется по длине заготовки, а не по диаметру. Но если порошок твердого сплава спрессовался по направлению длины заготовки сильнее, чем по ее наружному диаметру, то после спекания заготовка меньше изменится именно по длине (т. е. по шагу), чем по диаметру. Вот почему К. У. при расчете резьбовых работ недействителен.
После нескольких опытов я вывел определенную формулу для сплава ВК6М при изготовлении резьбовых калибров: шаг сырого калибра должен равняться шагу чертежному, умноженному на величину К. У. минус 0,025.
Шаг резьбы на кольцах после спекания стал получаться правильный.
Так были решены все три вопроса. В течение полугода мне удалось, работая урывками, изготовить около 100 калибровых резьбовых колец разных размеров.
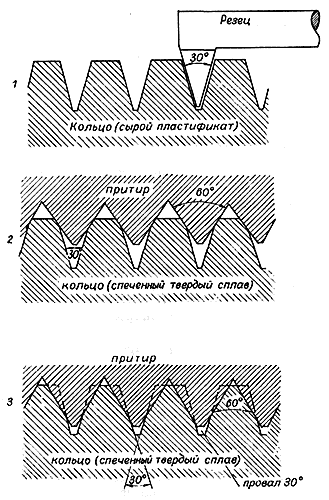
Схема нарезания и доводки резьбы калибрового кольца из твердого сплава (авторское свидетельство № 219798)
Надо прямо сказать, что в успех моей затеи никто не верил. Мастера, технологи, начальник техотдела, начальство цеха — все были недовольны, что я занимаюсь «пустым делом», отвлекающим от «настоящей» работы на план. Я их прекрасно понимал.
Искатель-рабочий в инструментальном деле был просто невыгоден цеху. Инструмент для металлообработки нужен тысячам заводов. Любой начальник цеха, любой мастер прекрасно понимает, что успех его рабочего-изобретателя в области нового инструмента не может долго принадлежать только одному заводу, он неизбежно станет достоянием всех заводов. Значит, изобретателю придется отрываться от своей основной работы для помощи по внедрению новшества на многих заводах страны или для налаживания серийного выпуска его изобретения на каком-нибудь специализированном заводе, а высококвалифицированных станочников не хватает на каждом заводе. Как же отпускать на другие заводы самого, может быть, нужного рабочего только потому, что ему взбрело в голову что-то изобрести! Ведь в план эта работа не зачтется, а отсутствие новатора даже в течение 10 дней может поставить под угрозу выполнение плана данного месяца.
Я знаю рабочих-изобретателей, которые не решились обострить отношения со своим начальством, а теперь горько сетуют на то, что их изобретение нигде не внедряется, и совершенно искренне заявляют, что они больше не будут ничего изобретать, чтобы не испытывать новых огорчений.
Что же лучше: испортить отношения с местнически настроенным начальством и добиваться широкого внедрения своего изобретения или прекратить творческую деятельность и остаться на хорошем счету у своего начальства? Я подчеркиваю, что речь идет о серьезной творческой работе. Мелкие усовершенствования местного цехового характера принимаются обычно руководством более или менее благосклонно и не вызывают негодования.
У рабочего-изобретателя есть еще один путь; бросить свою профессию, уйти со станка на какую-нибудь «легкую» работу — технолога или контролера. Тогда он получит некоторую свободу действий и будет иметь возможность «толкать» свое изобретение.
Прежде чем выбрать один из вариантов, каждый рабочий-изобретатель должен посоветоваться со своей совестью.
Уйти со станка? Но ведь каждый квалифицированный рабочий в глубине души всегда гордится своей профессией создателя материальных ценностей, и уход со станка воспринимается им как дезертирство. По-моему, ни один рабочий-коммунист, ставший изобретателем, не уйдет со станка ради внедрения своего изобретения. Он знает, что значит сейчас для цеха потерять хотя бы одного опытного станочника.
Значит, остаются два пути: или прекратить работу по внедрению своего изобретения, или нажить большие неприятности от своего разгневанного начальства. Я останавливаюсь на этом вопросе потому, что на распутье оказывались уже многие мои товарищи рабочие-изобретатели и в Москве, и в других городах. И еще потому, что с этими же вопросами придется столкнуться молодым искателям нового, которые будут нашей сменой, новым поколением рабочих-изобретателей.
Земля русская издавна славится рабочими-умельцами, и я уверен, что никакие трудности не остановят их творческого движения по пути технического прогресса. Но рассказать о том, как порой приходится добиваться внедрения своего изобретения, по-моему, все же надо. Это пригодится моим молодым коллегам, ставшим на трудный, но увлекательный и полезный всему народу путь искателя нового.
Трудно еще рабочему-изобретателю, а тем более коммунисту выбирать один из двух указанных выше путей. Коммунист не может не творить, он должен быть всегда правдивым, решительно подвергать критике недостатки, говорить правду в глаза любому начальству, искоренять подхалимство и другие пережитки прошлого.
После некоторых колебаний я выбрал опасный путь, понимая, конечно, на что шел. Захватив с собой несколько штук твердосплавных резьбовых колец, я пошел к главному инженеру Хитрину. Внешне кольца были не совсем обычными, но имели красивый и, что называется, торговый вид. Тонкий ободок твердого сплава с резьбой был впрессован в алюминиевую обойму, соответствующую гостовским габаритам кольца. Обойма анодирована в черный цвет, и на ее блестящей поверхности нанесены пантографом размер кольца и дата его выпуска.
Хитрин повертел в руках мои кольца.
— Ну и что же ты от меня хочешь, Данилов? — спросил он.
Я хочу подать заявку на изобретение под названием «Способ изготовления твердосплавных резьбовых колец». Для этого нужно ваше заключение о полезности способа, — ответил я. — Начальник центральной измерительной лаборатории считает, что по стойкости они раз в 200 превосходят обычные стальные кольца и обладают еще целым рядом преимуществ.
Я ожидал, что Хитрин поднимет трубку телефона,и спросит начальника лаборатории или начальника какой-нибудь другой службы завода, ведающей мерительными инструментами, о ценности моих колец. Но произошло нечто совсем другое.
— Ты знаешь, Данилов, — сказал Хитрин, — недавно один мастер механического цеха предложил какой-то станочек для навивки пружин. Механик цеха и старший мастер дали заключение, что этот станочек очень ценный и необходим цеху. Я им поверил и выдал автору 50 рублей. А потом оказалось, что этот станок никому не нужен и по сей день стоит в углу цеха, где собирают утиль… Ты иди, я пришлю в цех свое решение!
Я прождал четыре месяца, потом позвонил главному инженеру. Через секретаря Хитрин сообщил, что свое заключение он послал начальнику цеха Романову, чтобы он передал его мне.
Николай Александрович Романов, человек деликатный, несколько замялся, когда я его спросил о заключении Хитрина.
— Видишь ли, Борис Федорович! — начал Романов. — Я давно хотел показать тебе это заключение, да все как-то не решался тебя огорчать. На-ка вот, прочти! — и он подал мне бумагу.
Там было написано буквально следующее:
«В предложении Данилова нет никакой новизны, все это давно известно. Кольца не дают никакой экономии производству. На основании изложенного заявка не будет послана в Комитет изобретений и открытий. В случае, если автор пошлет заявку лично, бризу завода приказываю сообщить в Комитет изобретений о вышеизложенном заключении.
Хитрин».
Так весь мой двухлетний труд, все мои творческие замыслы в этой области были перечеркнуты одной размашистой подписью. Изобретателя с менее крепким здоровьем после такой резолюции мог хватить инфаркт. Я тоже чувствовал себя неважно и видел, как сочувственно смотрел на меня Романов.
— Брось все это дело, Борис Федорович, — произнес Романов, — ты у нас лучший специалист, мы тебя очень ценим, работай себе спокойно на своем станке и не порти зря кровь!
Признаюсь, такая мысль порой мелькала и у меня. «Плетью обуха не перешибешь» — говорит старая русская пословица. Но я вспомнил также изречение одного древнего мудреца: «Ты хочешь меда, так жала не страшись!»
И борьба продолжалась. В этой борьбе была доля чисто спортивного интереса. Но главным было горячее желание помочь нашей инструментальной промышленности. Я посоветовался с Евгением Александровичем Майкапаром.
— Что ж, — сказал Майкапар, — можно подать заявку лично, без завода. Нужно только приложить заключение другого солидного завода, ну, скажем, завода «Калибр», и каких-нибудь не менее солидных научно-исследовательских институтов.
В работе Московского совета новаторов принимала участие группа ученых из Особого конструкторского технологического бюро Госкомитета по делам изобретений и открытий. «Командовал» этим бюро известный ученый профессор Погодин-Алексеев. Бюро проводило работы по расширению сферы применения алмазов в обработке твердых сплавов. Мы часто советовались по этим вопросам, и я попросил ОКТБ дать свое заключение по моим кольцам. Ученые заверили, что заключение будет положительное, слишком очевиден эффект новых колец. Однако заключения не дали. Как я узнал потом, руководители ОКТБ побывали на нашем заводе, с которым бюро было связано договором, и встретились с главным инженером. После этого они отказались дать заключение ввиду того, что это, видите ли, «не их профиль».
Все было понятно без объяснений. Между тем я продолжал вечерами работать над дальнейшим усовершенствованием своих колец. Благодаря широким связям и знакомствам с работниками множества заводов мне удалось выявить ряд дополнительных полезных свойств твердосплавных колец.
На некоторых заводах радиопромышленности не могли пользоваться обычными стальными калибровыми кольцами. Оказывается, при навинчивании резьбового кольца на резьбу детали для проверки взаимозаменяемости деталь чуть-чуть намагничивалась от трения. Однако этого незначительного намагничивания было достаточно, чтобы прибор при работе искажал сигналы. Поэтому приходилось пользоваться калибровыми кольцами, сделанными из немагнитных металлов. Резьбовые кольца на этих заводах делали из латуни, бронзы или нержавейки. Эти металлы антимагнитны, но стойкость их в работе не превышает нескольких минут. Кроме того, неизбежные заусенцы на резьбе колец из этих мягких материалов не давали возможности точно замерить резьбу на деталях. Для таких заводов мои кольца оказались просто находкой. Твердый сплав марок ВКЗМ и ВК6М антимагнитен, и в то же время резьбовое кольцо, сделанное из этого материала, практически почти вечно.
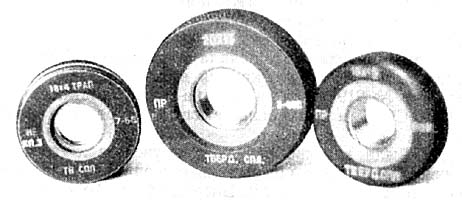
Резьбовые кольца-калибры из твердого сплава
На других заводах очень быстро выходили из строя стальные резьбовые кольца в цехах защитных покрытий. Там резьбовые детали надо постоянно проверять после покрытия, калибровые кольца все время работают в парах различных кислот и очень быстро покрываются коррозией. Доведенные поверхности твердого сплава почти не подвержены коррозии, а оболочка кольца из анодированного алюминия также не восприимчива к коррозии.
Но все эти работы я делал на других заводах. На родном предприятии на мои твердосплавные кольца было наложено табу, и я изготовлял только обычные стальные калибры.
Несколько лет подряд я оказывал посильную помощь и давал консультации по точным резьбовым работам во Всесоюзном технологическом институте приборостроения. Научный сотрудник института Вера Иосифовна Лесная приняла горячее участие в моих тяжких делах с заявкой на изобретение по твердосплавным кольцам. Она изучила технологию их изготовления. С ее помощью институт приборостроения дал хорошее деловое заключение о моем способе.
Руководство завода «Калибр» также дало положительное заключение о новизне и полезности моего метода изготовления твердосплавных колец.
Через три года после начала моей борьбы Комитет по делам изобретений и открытий выдал авторское свидетельство № 219798. Мои кольца были выставлены на ВДНХ СССР и удостоены высшей награды — золотой медали.
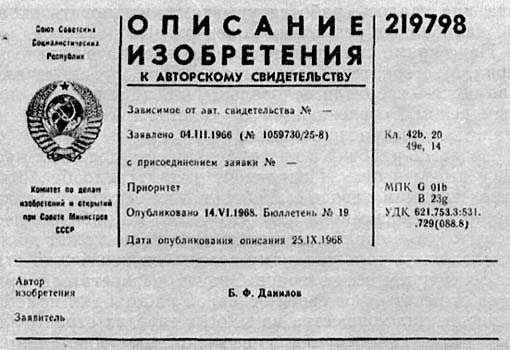
Это была, конечно, победа, и я чувствовал удовлетворение. И все-таки это была только первая и самая легкая часть труда изобретателя. Впереди была более трудная задача:внедрение.
Через некоторое время Хитрину пришлось расстаться со своим постом. На его место был назначен молодой ученый, кандидат технических наук Юрий Сергеевич Рудаков. После этого новаторские дела на заводе пошли несколько лучше. Однако запрет Хитрина на твердосплавные резьбовые кольца остался в силе, и на заводе «Знамя труда» по сей день несколькими экземплярами их работают только в двух цехах, а другие механические цехи про них и не знают.
В 1972 г. руководители Куйбышевского политехнического института прослышали про мои новые калибры и по заданию Министерства автомобильной промышленности включили эту тему в план научных работ для оснащения такими калибрами автомобильных заводов. Большую помощь в организации работы по внедрению новых калибров оказал давнишний друг новаторов — управляющий делами Министерства автомобильной промышленности Евгений Александрович Устинов.
А в 1973 г. руководитель этой темы, кандидат технических наук С.Я. Сагалович, прислал на наш завод документ, в котором говорилось, что, используя два моих изобретения, институт внедрил твердосплавные резьбовые калибры на двенадцати автомобильных заводах и что экономический эффект от этого составил, по подсчетам института, 100 тысяч рублей в год.
Так два изобретения нашли своего потребителя. Ну что ж, шесть лет не такой уж большой срок для внедрения изобретения.