ПОЛСОТНИ РАЦИОНАЛИЗАТОРСКИХ ПРЕДЛОЖЕНИЙ
ПОЛСОТНИ РАЦИОНАЛИЗАТОРСКИХ ПРЕДЛОЖЕНИЙ
Примерно к 1956 г. на моем счету было уже 50 рацпредложений. Не могу сказать, что все они были очень ценные, но все касались новых видов инструмента для получения резьбы или улучшали технологию изготовления различных инструментов. И я подумал, что мои инструменты могут быть полезны не только на нашем заводе. Но как их внедрить на других предприятиях, об этом я не имел ни малейшего представления.
Вот некоторые из моих рационализаторских предложений, которые, как потом оказалось, стали полезны многим машиностроительным заводам нашей страны.
Способ изготовления мерительных цанг. Во многих современных машинах есть различные узлы, подача в которых осуществляется движением поршня в цилиндре — обычное гидравлическое соединение.
Для того чтобы такие соединения были достаточно надежны и действовали безотказно, нужно, чтобы зазор между цилиндром и поршнем, работающим в масляной среде, составлял 5-7 микрон. Такова теоретически обоснованная задача, поставленная конструктором.
А как на практике при изготовлении этих систем гарантировался зазор в 5-7 микрон? Да никак или просто «на щуп»!
Присмотревшись в механических цехах к технике доводки поршня и внутренней поверхности цилиндра, я сделал для доводчиков гладкие калибры через каждые 2 микрона, чтобы они могли точно измерять внутренний диаметр цилиндра и иметь хоть какой-то ориентир. Но такие калибры — это, конечно, примитив. Ведь цилиндр мог иметь эллипс или бочкообразность в 2-4 микрона, которые никаким калибром не прощупаешь.
Наши снабженцы закупили пневматические длинномеры — ротаметры и четырехшариковые нутромеры конструкции завода «Калибр». Судя по рекламе и паспорту, оба прибора гарантировали точность замеров внутренних диаметров до 0,001 мм. Это было все, что современная измерительная техника создала для внутренних измерений с точностью до одного микрона. Но оба прибора не прижились у нас на заводе. Дело в том, что многие цилиндры имели в стенках отверстия и пользоваться пневматическим калибром для их измерения было невозможно — воздух выходил в эти отверстия.
Четырехшариковые нутромеры также не годились, так как ограничивали глубину замера 30-40 миллиметрами, а нам надо было измерять цилиндры гораздо длиннее. Кроме того, шарики нередко западали в отверстия цилиндра, а тогда вытащить нутромер из цилиндра было очень трудно. С такими мерителями ни о каких микронах нечего было и думать.
Контрольный мастер Н. С. Петров предложил новый прибор — цанговый нутромер для замера глубоких отверстий с точностью до 0,001 мм. Теоретически прибор обеспечивал требуемую точность, не требовал подводки специально очищенного сжатого воздуха, не западал в боковые отверстия цилиндра, был очень портативен: можно было, что называется, «носить микрон в кармане». Он был нужен очень многим заводам.
Николай Сергеевич Петров обращался во многие инструментальные цехи различных заводов, ездил и на завод «Калибр» с просьбой изготовить хоть один опытный экземпляр его прибора. И везде специалисты ему отказывали, говоря, что сделать из металла нарисованное им на бумаге невозможно. Маялся он со своим нутромером уже несколько лет. И наконец чертеж нутромера однажды попал ко мне.
Все в этом приборе было просто, за исключением одной детали — мерительной цанги. Для того чтобы гарантировать точность измерения в один микрон, эта цанга должна быть изготовлена, естественно, с еще большей точностью! Никакими, даже сверхзолотыми руками добиться такой точности при сложной конфигурации невозможно. Надо было найти такую технологию, при которой все элементы цанги получались бы правильно.
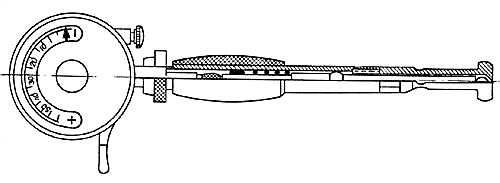
Цанговый нутромер изобретателя Н.С. Петрова
Я решил попытаться создать технологию изготовления мерительной цанги нутромера. Полгода отрабатывал эту технологию. Потом еще полгода доводил ее до дела на станке. И наконец через год эти мерительные цанги стали делать мои ученики. А через два года цанговый нутромер уже появился на многих приборных заводах.
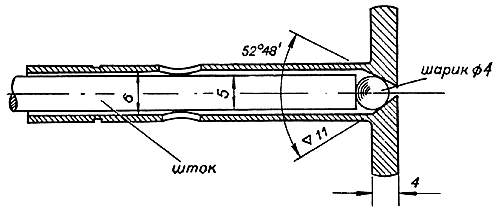
Самое сложное при изготовлении мерительной цанги — сделать глубокий точный конус с углом 52°48’
Меня не раз приглашали на заводы, чтобы показал процесс изготовления мерительных цанг. Значит, нужда в этом приборе не исчезла и в настоящее время. Однако руководители завода «Калибр», видимо защищая честь мундира, категорически отказались от массового выпуска цангового нутромера Петрова — «чужое» детище! Поэтому и сейчас на ряде заводов делают нутромеры для себя своими силами, а пользоваться приборами завода «Калибр» избегают. Завод «Калибр» создал и выпускает массу очень сложных приборов и точнейших инструментов, а вот с нутромером большой точности ему не повезло.
Цанговый нутромер работает методом сравнения с установкой заданного размера по эталонному кольцу. В отдельных случаях размер можно устанавливать по блоку концевых мер (не ниже 3-го разряда), зажатых в мерительную струбцину. Прибором можно проверять с точностью до 0,001 мм отверстия глубиной до 150 мм, а при диаметре отверстия свыше 25 мм — и более глубокие. С такой же точностью можно проверять конусность и эллипсность отверстия на всю его глубину.
Цанговый нутромер состоит из микрометра с ценой деления 0,001 мм; корпуса, в котором движется шток; мерительной цанги и шарика. Цанги делаются сменные, с градуировкой по наружному диаметру через каждый миллиметр. Наименьший диаметр, измеряемый прибором, 6 мм, наибольший — 52 мм. По конструкции прибор очень прост.
Самое сложное при изготовлении мерительной цанги — это получение глубокого точного конуса с углом 52°48’ с чистотой обработки по 11-му классу. Не менее сложно и важно выполнить наружный эллипс с весьма точными радиусами, а также добиться строгой концентричности элементов конуса, эллипса и радиусной поверхности.
Угол конуса внутри цанги рассчитан математически, он обеспечивает перемещение штока на один микрон при изменении наружного диаметра мерительной сферы цанги точно на один микрон. Для правильного изготовления цанги необходимо прежде всего правильно выполнить все предварительные операции, так как без этого даже самой тщательной доводкой нельзя добиться требуемой точности прибора.
Многие мои рационализаторские предложения касаются режущего инструмента. Из них хочется познакомить читателей с изменениями технологии изготовления метчиков и плашек, которые требуются на каждом машиностроительном заводе и выпускаются в СССР десятками тысяч.
Технология изготовления метчиков общеизвестна:
1) заготовка,
2) нарезка резьбы (под резьбошлифовку или начисто в размер),
3) фрезеровка канавок,
4) термообработка,
5) резьбошлифовка (если резьба нарезана с припуском на шлифовку),
6) заточка.
Первые (черновые) метчики и метчики со сложным фасонным профилем резьбы обычно нарезаются начисто в сыром виде. Такая технология существует много десятилетий, и даже сейчас многие инструментальщики сделают круглые глаза, если им сказать, что ее надо изменить. А изменить эту технологию обязательно надо! Я предложил только поменять очередность двух операций, и этого оказалось достаточно, чтобы стало возможным выполнение норм токарем на 1000%. Тысяча процентов — это звучит неправдоподобно, но никакого преувеличения здесь нет.
Возьмем для примера метчики с фасонной круглой резьбой, которые на большинстве заводов нарезаются сразу начисто в размер в сыром виде (такая резьба применяется в устройствах пожарного дела и в арматуре).
По норме на нарезку круглой резьбы метчика диаметром 20 мм с шагом 3 мм и длиной нарезки 50 мм полагалось на нашем заводе 29 минут — как говорится, не очень-то разгуляешься! Ведь надо выдержать размер двух радиусов, наружный и внутренний, диаметр резьбы, да еще надо чистоту поверхностей резьбы держать в пределах 7-го класса.
Нарезать круглую резьбу затруднительно еще потому, что стружка налипает на резьбовую гребенку по всему профилю, а это неизбежно влечет за собой надиры и срывы на наружном радиусе резьбы. Чтобы избежать надиров, мы нарезали метчики гребенкой, зажатой в пружинную державку, но и это далеко не всегда помогало.
Я поменял местами вторую и третью операции: фрезеровку канавок предложил делать по заготовке, а резьбу нарезать потом.
И мастера и технологи, конечно, вытаращили на меня глаза и стали наперебой доказывать, что, дескать, нарезка пойдет на удар, будет скалывать гребенку, а пружинная державка с гребенкой будет все время «кивать»!
Однако я настоял на своем и на первой же партии в 100 штук выполнил норму на 1000%: на изготовление каждого метчика у меня пошло 2,9 минуты. И никакого чуда тут не было, теоретически все было обосновано и осмыслено заранее. Прежде всего, я отказался от пружинной державки, а гребенку зажал в стальной жесткий брусок с отверстием под болт. Такая жесткая державка никаких «кивков» не давала при нарезке на удар.
При нарезке старым методом на резьбе часто получались надиры, и, чтобы их избежать, приходилось работать на малых скоростях. При новом способе (нарезка на удар) я увеличил скорость в 10 раз и, по существу, нарезки «на удар», как таковой, не стало: при обдирке резьбы стружка сливалась в сплошную короткую толстую ленту.
Из-за чего получались надиры на резьбе при старом методе? Из-за стружки, налипающей на гребенку. При новом методе такое налипание стружки прекратилось само собой. Стружка, конечно, налипала по-прежнему, но теперь, прежде чем начиналось резание, каждое перо метчика сшибало налипшую стружку с гребенки.
Впоследствии я все это проанализировал, когда, пустив станок на малые обороты, рассмотрел под лупой работу гребенки новым методом. Тогда же, изменяя технологию, я руководствовался только интуицией и большим опытом нарезания всевозможных резьб на самых разнообразных режущих и мерительных инструментах.
Сперва против новой технологии пытались возражать некоторые резьбовики и механики. Но преимущество нового метода было столь очевидно, что скоро все резьбовики стали требовать, чтобы им давали на нарезку метчики с заранее фрезерованными канавками.
Через две-три недели ко мне пришли заточники, чтобы поблагодарить. «Как легко и быстро стало теперь затачивать метчики!» — сказали они. Я их отлично понимал: раньше, когда канавки метчиков фрезеровались после нарезки резьбы, фреза загибала в резьбу большие заусенцы, и заточнику приходилось абразивным кругом много снимать металла с каждого пера для того, чтобы вывести эти заусенцы. Теперь же заусенцы исчезли, и заточка пошла в 3 раза быстрее.
Новой технологией стали пользоваться резьбовики, изготовляющие метчики с обычной метрической резьбой: черновые метчики стали нарезаться «на удар» сразу начисто в размер, чистовые нарезались «на удар» с припуском под резьбошлифовку.
Вскоре я услышал благодарность и от резьбошлифовщиков, чего, признаться, не ожидал. Казалось бы, не все ли равно резьбошлифовщику, когда была нарезана предварительно резьба — до фрезеровки канавок или после фрезеровки. Оказалось — далеко не все равно. Резьбошлифовщик попадает абразивным кругом в нитку резьбы «на искру» — «чиркнет» по одной стороне профиля, увидит искру и заметит этот момент по индикатору продольного хода, потом подведет круг к другой стороне профиля до получения такой же искры. Увидит на индикаторе, сколько от одной стороны профиля до другой, и поделит эту величину пополам. После этого поставит резьбовой круг точно посередине (по индикатору) и начинает шлифовать профиль резьбы — он уверен, что попал в нитку точно посередине.
При прежнем методе искра получалась от соприкосновения шлифовального круга с заусенцем, оставшимся внутри профиля резьбы после фрезеровки, а не с плоскостью профиля. Поэтому резьбошлифовальный круг не всегда попадал точно посередине нитки резьбы, рабочий шлифовал только одну сторону резьбы, а другая оставалась черной — и метчик шел в брак.
Теперь же заусенцев не стало, искра получалась только от прикосновения круга к самой плоскости резьбы, и попадание в нитку стало всегда точным. Брак полностью прекратился.
Несколько слов о выполнении норм на 1000% при нарезании чистовых метчиков с круглой резьбой.
Конечно, только одна перестановка очередности операций не могла дать такого высокого результата. Здесь довольно важную роль сыграли разные мелочи, применение которых позволило без суеты, но быстро и уверенно произвести две операции — прорезку (обдирку) профиля и чистовую нарезку резьбы.
На каждую операцию было затрачено в среднем по полторы минуты. К таким «мелочам» относятся, как я уже сказал, отказ от пружинной державки, твердосплавный (не вращающийся) задний центр, кернение (пометка) одной из сторон квадрата метчика под хомутик и др.
С простым (стальным) задним центром увеличить скорость резания в 10 раз было бы невозможно — сгорел бы. Вращающийся же центр не дает устойчивости и достаточной жесткости при нарезке «на удар», изделие стало бы вибрировать. Применение твердосплавного центра все это ликвидировало.
Пометка одной стороны квадрата метчика позволяла зажимать хомутик всегда в одно место, что избавляло токаря от необходимости попадать в нитку резьбы после обдирки чистовой гребенкой. Достаточно было попасть в нитку первый раз — и остальные 99 метчиков уже не нуждались в этой операции.
Применение подобных мелочей в комплексе с новой технологией и позволило даже теперь, когда, казалось бы, все уже учтено и рассчитано, выполнить норму на 1000%.
Что касается применения новой технологии для изготовления круглых плашек, то и в этом случае тоже был получен значительный эффект.
По обычной технологии нарезка внутренней резьбы шла медленно, так как при непрерывной стружке опасность появления надира на резьбе плашки была еще больше, чем при нарезке наружной резьбы. По предложенной мной технологии в круглых плашках сперва сверлят окна, затем растачивают отверстие под нарезку, потом снимают затылок на перьях плашки с обеих сторон и только после этого нарезают резьбу.
Нарезать таким образом плашки я начал с размера 24?1,5 и 24?2 и дошел до размера 100?2. Нарезку вел «на удар» с большой скоростью при постоянном «сшибании» стружки, налипающей на зубья гребенки. Резьба получалась в 2 раза быстрее и чистая, без малейших надиров.
Кроме повышения производительности на самой операции нарезки резьбы выявились и некоторые другие преимущества нового метода: отпала необходимость в изготовлении маточных метчиков на каждый размер плашки; стала ненужной операция прогонки плашки маточными метчиками для снятия заусенцев в резьбе был ликвидирован брак по резьбе, который возникал во время прогонки резьбы маточным метчиком.
Конечно, так же как и при нарезке метчиков, все эти успехи не пришли сами собой, только от перестановки операций в технологии. Для внутренних гребенок пришлось сделать державки повышенной жесткости, а сами гребенки для нарезки новым методом стали делать с хвостовиком большого диаметра. Кроме того, гребенки для нарезки плашек я предложил делать не с обычным профилем, а с конусом по среднему диаметру, в то время как обычные резьбовые гребенки имеют профиль резьбы, нарезанный по цилиндру с конусом по наружному диаметру.
У обычных гребенок острием работает только один последний зуб, который быстро затупляется, и гребенку часто приходится перетачивать. При определенном угле конуса, различном для разных шагов резьбы, каждый зуб модернизированной гребенки режет всем профилем и снимает при этом весьма малую стружку, что предохраняет инструмент от затупления и обеспечивает легкий отход стружки. Такая гребенка с четырьмя зубьями снимает за один проход слой металла глубиной 0,2 мм по диаметру.
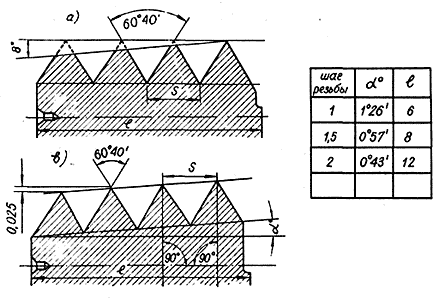
Профиль обычный (а) и усовершенствованный (в) гребенки для нарезания плашек
Раньше резьбовики зачастую раздумывали — прогонять маточным метчиком плашку после сверления окон или не прогонять? Если прогонять, то это значит рисковать плашкой, так как не всегда удается сразу попасть в нитку резьбы метчиком (особенно при большом диаметре). А сразу не попал — плашка идет в брак. Если же не прогонять, то заточники поднимут крик, так как им приходится долго стачивать перья плашки, чтобы удалить заусенцы на резьбе, оставшиеся после сверления окон. Часто при этом резьба отжигалась, становилась мягкой — и плашка опять шла в брак. Так и этак — все равно было плохо!
По новой технологии все эти неприятности отпали, плашки стали получаться высокого качества и вдвое быстрее.
Так незначительное на первый взгляд изменение порядка операций в технологии дало блестящий результат. Сейчас по этому методу работают в инструментальных цехах многих заводов. Тем инструментальщикам, которые работают по-старому и режут резьбу на плашке «по целому», я советую перейти на новую технологию, они не прогадают!
Описывать все свои 50 рационализаторских предложений я, конечно, не буду — это и долго да и незачем. Но еще об одном предложении, облегчившем тяжелый физический труд токарей-доводчиков, я расскажу — о механизации доводки резьбовых калибровых колец средних и больших размеров.
В большинстве инструментальных цехов машиностроительных заводов калибровые резьбовые кольца нарезают резцом и после закалки доводят чугунными притирами. Шлифование внутренней резьбы на калибрах применяется довольно редко.
Если взять, например, кольцо М100?2, то припуск на доводку обычно оставляют 0,4 мм. А если учесть, что после термообработки кольцо неизбежно деформируется на 0,3-0,35 мм, то токарю приходится долго доводить кольцо при помощи притиров, затрачивая много физической силы.
Мне удалось механизировать доводку больших резьбовых калибровых колец, использовав для этого обычный токарный станок. Первый опыт я проделал с кольцами диаметром от 60 до 200 мм, причем станок для этой цели использовал старый, предназначенный к списанию.
Между направляющими станка на ребрах станины прикреплена планка с продольным пазом. По этому пазу перемещаются и могут быть закреплены в нужном месте два кнопочных пускателя правого и левого хода. Кнопки пускателей удлинены и направлены навстречу друг другу.
Резьбовое кольцо навертывается на притир обычным порядком и зажимается болтом водила. Хвостовик водила, перемещаясь вместе с кольцом вдоль оси притира, в своем крайнем положении нажимает на левую кнопку пускателя, переключающую станок на обратный ход. Дойдя вместе с кольцом до правой кнопки пускателя, водило переключает станок на прямой ход. Так автоматически происходит реверсирование вращения шпинделя, а вместе с ним и изменение направления движения кольца вдоль притира. Чтобы хвостовик водила мягче ударялся об упоры в крайних положениях, внутри станины прикреплены два бруска из текстолита.
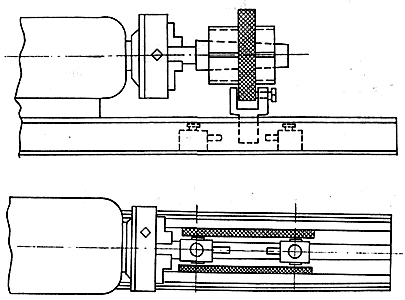
Приспособление на токарный станок для механической доводки резьбовых калибров
Обычный резьбовой притир сажают на конусную оправку, и токарю остается только следить за нормальным движением кольца по притиру, время от времени добавлять притирочный абразив и, если кольцо стало слабо ходить по резьбе притира, поджать его на оправке. Таким образом, с кольца легко снимается припуск в 0,7-0,8 мм и резьба на кольце получается чистая. На окончательную доводку оставляют 0,03-0,04 мм и выполняют доводку вручную на чистовом притире с малым количеством более тонкого абразива.
Кроме резьбовых калибров-колец на модернизированном станке таким же образом можно доводить различные резьбовые детали, требующие удаления больших припусков на резьбе.
Поскольку пускатели для реверсирования вращения шпинделя при доводке поставлены ниже уровня направляющих станины (они являются дублерами основных пускателей станка), станок остается полностью пригодным для любых токарных работ и может быть использован по своему прямому назначению.
Мне удалось рационализировать и усовершенствовать целый ряд резьбовых работ и инструментов, но особой моей заслуги в этом нет: просто тогда было еще велико различие в культуре инструментального производства в Москве и Ленинграде. Я многое узнал на ленинградских заводах, и то, что там было обычным делом, на московских заводах зачастую оказывалось новшеством.
Больше книг — больше знаний!
Заберите 20% скидку на все книги Литрес с нашим промокодом
ПОЛУЧИТЬ СКИДКУ