ПЕРВЫЕ ШАГИ НА МОСКОВСКОМ ЗАВОДЕ
ПЕРВЫЕ ШАГИ НА МОСКОВСКОМ ЗАВОДЕ
Начальник инструментального цеха Владимир Иванович Ефимов отнесся ко мне хорошо. Чувствовалось, что он доволен моими теоретическими знаниями производства инструмента, но, видимо, сомневается, удастся ли мне как следует работать на станке. Он предложил работать на любом станке, который мне подойдет, но то и дело посматривал на мою искалеченную ногу.
На всех лучших станках работали местные специалисты, и мне не хотелось лезть к ним во вторую смену. Кроме того, я понимал, что на большом станке придется работать стоя, а это у меня вряд ли получится. Поэтому я довольно равнодушно прошел мимо отличных станков «Кергер» и остановил свой выбор на станке завода имени Воскова, на каком работал на заводе в Ленинграде. Станок был запущен, на нем не хватало некоторых деталей. В частности, только после долгих поисков я нашел коррекционную линейку к нему, которую местные специалисты выбросили, полагая, что она лишняя… Оборудовав станок всем необходимым, сделал для себя вращающийся стул и приступил к работе.
То ли я очень изголодался по любимому делу за годы войны, то ли уровень мастерства на этом заводе был несколько ниже, чем на тех ленинградских заводах, где мне пришлось учиться, только со второго месяца я стал выполнять норму на 400%. Тут, конечно, сыграли роль и некоторые уникальные инструменты, которые я привез из Ленинграда.
Кое-кто из работников бросал косые взгляды, иногда отпускал обидные словечки, но по этому поводу я особенно не расстраивался. Пройдя хорошую школу знатных ленинградских стахановцев Коптелова и Художникова, я уже не боялся чужих мнений, тем более что в большинстве своем рабочие отнеслись ко мне хорошо, а порой даже удивлялись: «Вот солдат дает прикурить!»
Завод в то время серийно выпускал очень сложные и точные машины, и взаимозаменяемость резьбовых соединений обеспечивали резьбовые калибры, которые мы делали. Квалифицированных токарей на заводе не хватало, и работать приходилось часто по две смены. Все трудились с большим подъемом: ведь шел последний год войны, и уже чувствовалось приближение дня окончательной победы. Работы было по горло, но это не удручало, а, наоборот, поднимало дух. Несмотря на больную ногу, работал с увлечением и одновременно обучал нескольких учеников.
В цехе меня в шутку называли «резьбовых дел мастером», но я занимался не только резьбой: на меня свалились почти все сложные доводочные работы.
Приобщение к рационализаторской деятельности произошло как-то само собой. Сейчас я даже не могу вспомнить, как стал рационализатором.
По-моему, рабочий становится рационализатором вследствие стечения самых разнообразных, порой случайных обстоятельств. У меня обстоятельства были такие: я много поработал на передовых ленинградских заводах, видел много различных инструментальных цехов, у больших питерских специалистов токарного дела научился работать. И мне, естественно, захотелось здесь, в Москве, применить более совершенные технологические приемы, более производительный инструмент ленинградских специалистов.
Я стал понемногу изменять то один, то другой техпроцесс, а оказалось, что такие изменения, повышающие производительность труда или качество изделий, и есть рационализация. Так я стал рационализатором.
Мне казалось, да и сейчас я так считаю, что в нашей стране рационализацию надо приветствовать и поддерживать. Поэтому в голове никак не укладывалось то, что некоторые руководители инструментального цеха решительно выступали против изменений технологии, установленной много лет назад. Мастер Крылов, например, прямо запрещал мне работать по ленинградской технологии, хотя, как специалист, он не мог не видеть, что «моя» технология гораздо производительнее старой. Действовала «инерция старой техники».
Я не отступал, мастер тоже был упрям, и в результате — скандал. Мастер, а он проработал на этом заводе 25 лет, пошел на прием к директору завода и, как мне потом рассказали, поставил вопрос «на попа»: «Или я, или Данилов, вместе нам не работать!»
Все-таки большинство руководителей в цехе рассудило правильно, по-советски. Меня поддержали мастера Н.М. Панов, А.И. Лычев, начальник центральной измерительной лаборатории (ЦИЛ) завода В.Н. Фалеев, некоторые токари (те, которым я успел передать кое-что из моего ленинградского опыта). Кончилось тем, что Крылова перевели на другой участок.
Завод, на котором я работал, в 1950 г. был объединен с другим предприятием, и теперь наш инструментальный цех стал огромным. С тех пор я здесь и работаю токарем и не собираюсь отсюда уходить до конца своей жизни. Завод стал для меня родным домом. Куда бы меня ни заносила судьба по изобретательским делам, всегда с радостью возвращаюсь в свой инструментальный цех, к моим ученикам и товарищам по работе.
В начале 50-х годов техническое творчество разделялось на три категории: рационализаторское предложение; техническое усовершенствование; изобретение.
Осуществив около 30 рационализаторских предложений, я решился на первое техническое усовершенствование. Хотя оно уже «история», я все-таки кратко расскажу о нем.
В то время наш завод выпускал много машин различных типов. Механические цехи изготовляли серийным порядком огромное количество самых различных деталей. Понятно, что инструментальному цеху приходилось делать много резьбовых калибров (пробок и колец) для контроля и соблюдения взаимозаменяемости деталей. Наша мастерская резьбовых калибров явно не справлялась с заказами механических цехов, а тут еще, как снег на голову, свалилось новое задание.
Для различных гидравлических систем требуется большое количество соединительных штуцеров с конической резьбой. И очень часто эти штуцеры текли. А каждый, кто имел дело с трактором, автомобилем или мотоциклом, знает, что это означает, если, скажем, масло или горючее протекает в стыках трубопроводов. Нужно было создать такое резьбовое соединение, которое не давало бы ни капли течи.
На помощь пришел ученый. Доктор технических наук Кацнельсон разработал новую нормаль на коническую резьбу, которая теоретически полностью исключала течь в гидросистемах.
По старой нормали «захлест» конической резьбы Бриггса шел по среднему диаметру (т.е. по плоскостям) резьбы, так же как у обычной цилиндрической резьбы. По внутреннему и наружному диаметрам резьбы оставались зазоры в несколько сотых миллиметра, по которым и вытекала жидкость, как бы туго ни затягивали штуцер. Новая нормаль предусматривала одновременный «захлест» конической резьбы по среднему, внутреннему и наружному диаметрам. Для этого наружная и внутренняя площадки резьбы делались мерные, с весьма малым допуском.
Теоретически все было правильно. Но для серийного выпуска штуцеров по новой нормали были нужны новые резьбовые калибровые кольца. Если раньше, при старой нормали, достаточно было одного резьбового калибрового кольца, измеряющего только средний диаметр резьбы, то теперь понадобилось еще и резьбовое кольцо, проверяющее только внутреннюю площадку резьбы. А эта площадка у резьбы Бриггса составляет всего 0,04-0,07 мм. Следовательно, внутренняя площадка резьбы у калибрового кольца должна быть еще меньше, т.е. 0,03-0,05 мм (в зависимости от шага резьбы). Это необходимо для того, чтобы калибровое кольцо проверяло только внутренний диаметр резьбы штуцера и не задевало за плоскости резьбы. Проверка наружной площадки конической резьбы не представляла сложности — она проверялась гладким конусным кольцом. Если резьба на всех штуцерах будет сделана по этим трем конусным кольцам и окажется в допусках, то можно гарантировать плотность резьбового соединения и ликвидацию течи в гидросистеме.
Изготовление калибрового хозяйства для конической резьбы по новой нормали поручили мне.
Для того чтобы резьба кольца не задевала плоскостей резьбы штуцера, она делается с углом 45°, в то время как резьба имеет 60°. Доводка резьбы такого кольца с внутренней площадкой в 0,03 мм поставила меня, видавшего виды лекальщика, в тупик. Ведь для того чтобы получить после доводки такую малую площадку на внутреннем диаметре резьбы, надо нарезать на чугунном притире наружную резьбу с внутренней площадкой меньше четырех сотых миллиметра, т.е. практически надо сделать резьбу с углом острым, как бритва.
Никаким резцом это сделать невозможно. Поэтому при доводке резьба «садилась» своим внутренним диаметром на притир, внутренний диаметр сразу «проваливался» — и кольцо шло в брак.
Я понимал, что мудровать над тем, как нарезать чугунный притир с резьбой по внутреннему диаметру до теоретического острия, бессмысленно. Нужно было принципиально новое решение. Оно пришло не сразу, а после довольно мучительных поисков. Надо сказать, что и это, и все последующие технические усовершенствования и изобретения рождались, что называется, в муках.
В данном случае дело осложнялось тем, что механический цех завода ждал от меня калибров, чтобы начать серийное изготовление деталей, а я топтался на месте и не мог решить задачу, на первый взгляд не такую уж и сложную.
Мой рабочий престиж висел на волоске: ведь на заводе я один имел 8-й разряд и больше обращаться было не к кому.
Несколько вечеров я ломал голову и в конце концов создал новый вид резьбового притира — притир с полуходовой резьбой. Чтобы его понять, надо знать, что такое шаг резьбы и что такое ход резьбы. Шаг — это расстояние между соседними нитками резьбы, а ход резьбы — расстояние, на которое перемещается гайка вдоль винта при повороте на один оборот.
В обычной одноходовой резьбе шаг равен ходу. Если резьба имеет два захода (двухзаходная) — то ход равен двум шагам резьбы, если три захода — то трем шагам, и т.д.
Новый притир имел полуходовую резьбу. На первый взгляд это кажется невероятным: притир имеет резьбу с шагом 3 мм, а на него легко и плавно навинчивалось кольцо с шагом 1,5 мм. Ведь всем токарям известно, что если резьба на кольце будет с шагом не 3 мм, а хотя бы 2,9 мм, то оно никогда не навернется на резьбу с шагом 3 мм. А тут разница в шагах не 0,1 мм, а целых 1,5 мм, — и резьба хорошо свинчивается!
Однако такой, казалось, загадочный притир имеет большие преимущества. Притир нарезался не остроносым резцом, а резцом с площадкой у вершины, почти равной шагу резьбы. Так, при нарезке резьбы с шагом 1,5 мм площадка резца составляла 1,3 мм. Такая широкая площадка (вместо острия) позволяла брать при нарезании большие стружки без опасения, что у резца притупится острие. Нарезка выполняется следующим образом.
Токарный станок, оснащенный откидным верхним суппортом, настраивают на шаг резьбы калибра. На притире фрезеруют произвольно одну канавку. Резьбовой резец с площадкой у вершины, равной шагу резьбы минус 0,2 мм, вводят в канавку и, пройдя по шагу один оборот, прорезают в притире винтовую канавку шириной на 0,2 мм меньше шага резьбы. После этого резец отводят, откидывая верхний суппорт, и притир делает один оборот вхолостую. При следующем обороте резец опять вводят в канавку притира и нарезают вторую винтовую канавку, которая отстоит от первой на два шага резьбы калибра.
Таким образом, в результате чередования холостых и рабочих оборотов притира получают витки резьбы, отстоящие друг от друга на два шага резьбы, поставленной на станке.
При доводке калибрового кольца таким притиром внутренняя площадка профиля резьбы никогда не соприкасается с телом притира, она всегда «висит» над дном резьбы притира, и последний доводит кольца только по плоскостям резьбы, постепенно уменьшая ширину площадки до теоретического острия.
Доводка идет быстро, кольцо никогда не заедает и не дает засорений, так как отработанный абразив и чугунная пыль, отделяющиеся от притира, находят себе место в пустом пространстве, образованном срезанной ниткой.
После доводки плоскостей резьбы и получения острия на ее внутреннем диаметре гладким конусным притиром делается требуемая площадка.
Почему называется «притир с полуходовой резьбой»? При двухходовой резьбе гайка, навернутая на винт, перемещается вдоль за один оборот на расстояние двух шагов, а в моей полуходовой резьбе гайка перемещается за один оборот только на полшага резьбы винта.
Созданием такого на первый взгляд нелепого притира была решена проблема калибрового хозяйства для ноной нормали. Механический цех получил новые калибры и стал серийно выпускать штуцера. Течь в гидросистемах прекратилась, и больше по этому поводу жалоб никогда не было.
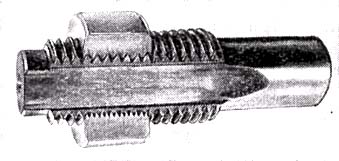
Притир с полуходовой резьбой
Впоследствии мне удалось еще более усовершенствовать притир для доводки конусных резьбовых колец. Надо сказать, что изготовление конусных резьбовых калибров (пробок и колец) любых наименований — одна из наиболее сложных инструментальных работ.
К нам на завод постоянно приезжают инструментальщики с различных предприятий страны, и многие — для того, чтобы ознакомиться с новыми конусными притирами. Обычно гости просят дать хоть один для образца. Приходится давать, а для себя делать новые. Ввиду интереса специалистов к этому небольшому новшеству, я считаю полезным рассказать и о нем.
Эта идея родилась так: я получил заказ на изготовление довольно большой партии конусных резьбовых калибровых колец для контроля балонной резьбы с углом 3°26’47'.
Когда я приступил к операции доводки, то после третьего кольца у меня заболели кисть и локоть правой руки, которой приходится держать кольцо. Доводка (т. е. съем на плоскостях резьбы припуска, оставленного для термообработки) обычного цилиндрического резьбового кольца происходит при движении кольца по всей длине притира. Притир внутри имеет конусное отверстие и сидит на гладкой конусной оправке. Притир имеет один продольный разрез, благодаря чему немного разжимается, т.е. в процессе работы может увеличиваться по диаметру, а следовательно, внутри резьбы доводимого кольца он двигается всегда с напряжением. Намазанный абразивной пастой, притир довольно быстро снимает припуск на резьбе кольца и придает ей зеркальный блеск.
Притир зажимается в патроне доводочного станка, а доводчик держит правой рукой обрабатываемое кольцо, не давая ему провернуться вместе с притиром. По мере увеличения диаметра кольца доводчик поджимает притир на конусной оправке, создавая постоянный напряженный контакт между резьбами кольца и притира.
При доводке конусного резьбового кольца картина процесса резко меняется: съем припуска на резьбе происходит не непрерывно, а только в момент захлеста кольца на резьбе притира. В этот момент рука доводчика испытывает сильное мгновенное напряжение из-за необходимости моментально остановить кольцо от проворачивания его в руке; доводчик должен сейчас же переключить мотор станка на обратный ход и опять сильно сжать рукой вращающееся вместе с притиром кольцо, чтобы сорвать его с захлестнувшей его резьбы притира, а затем опять повторить все сначала, моментально переключив станок на прямой ход. В общем, эта операция доставляет много неприятностей рабочему-доводчику.
Надо иметь в виду, что кольца по наружному диаметру имеют крупную накатку, которая при частом проворачивании кольца стирает кожу с ладони, а постоянный напряженный сжим и разжим кисти вызывает болезнь локтевого сустава — эпиканделит. Как и другие доводчики, я тоже болел этой болезнью по нескольку недель, и это случалось обычно после доводки конусных резьбовых колец.
Кроме напряженного физического труда доводка таких колец обычными притирами связана с рядом других чисто производственных отрицательных моментов. Очень трудно сохранить при доводке правильный угол конуса резьбы, так как кольцо, все время захлестываясь на одном и том же месте резьбы притира, «выкапывает», как говорят доводчики, на этом месте «лощину», и поэтому кольцо, упираясь в бугор после лощины, доводится очень медленно и без должного класса чистоты, так как непрерывного доводочного трения не получается. Ни о каком зеркальном блеске на резьбе не может быть и речи.
Доводочный станок приходится переключать с прямого на обратный ход прямо-таки молниеносно (иначе вообще никакой доводки не получится). От этого сильно перегревается, а случается, что и перегорает мотор станка. В общем, работа эта несладкая во всех отношениях, и все из-за притира. Вот я и решил еще раз изменить его.
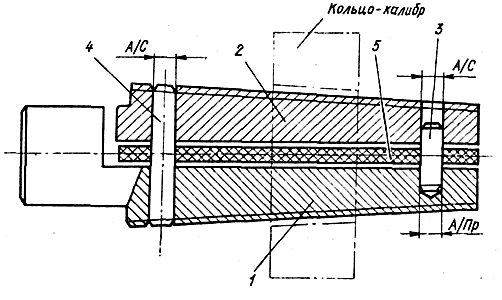
Усовершенствованный притир на коническую резьбу:
1 — основная часть притира;
2 — вторая половина притира;
3, 4 — шпилька, запрессованная в основную часть притира;
5 — прокладка из резины.
«Нужно сделать так, — рассуждал я, — чтобы конусное кольцо ходило по притиру, по всей его длине с постоянным напряжением, как если бы оно было не конусным, а цилиндрическим».
Решение оказалось настолько простым, что я потом удивлялся, как раньше до этого не додумался.
Теперь резьбовой притир для доводки конусных калибровых колец выглядит так, как показано выше на рисунке.
Перед нарезанием резьбы на притире в нем сверлят два отверстия под шпильки. После нарезки резьбы притир на фрезерном станке разрезают вдоль. В одну половинку притира запрессовывают две шпильки, на которые со скользящей посадкой надевается подвижная половинка. В образовавшийся от разрезки фрезой зазор закладывается эластичная (резиновая) прокладка такого размера, чтобы она сидела на шпильках, не выступая за внутренний диаметр резьбы (вместо резины можно использовать две пружины, надетые на шпильки).
Доводка ведется не толчками, а непрерывно. Кольцо, которое доводчик держит правой рукой, навинчивается на тонкий конец притира, и станок пускается на прямой ход; кольцо начинает двигаться по притиру к наибольшему диаметру, сжимая эластичную прокладку и сближая половинки притира. Взвесь абразива, которой смазаны обе части притира, увеличивает его трения по резьбе кольца и снимает с нее припуск.
После переключения станка на обратный ход кольцо идет к тонкому концу притира, а резиновая прокладка (или пружины, надетые на шпильки) разжимает обе части притира, поддерживая необходимый для доводки напряженный контакт резьбы притира и кольца.
Сейчас резьба на кольце доводится быстро и получает зеркальный блеск, так как кольцо ходит под напряжением по всей длине притира. Никакой «лощины» на притире не образуется, и конус резьбы калибра получается правильным; у доводчика перестает болеть правая рука; мотор доводочного станка не перегревается, так как теперь не нужно множество раз и моментально переключать его с прямого на обратный ход.
Примерно половина всех отрицательных явлений, относящихся к доводке конусных резьбовых колец, сопутствовала и доводке гладких конусных калибров (втулок типа конусов Морзе). Применение нового притира в виде двух гладких половинок конуса облегчило процесс доводки и гладких конусных калибров-втулок, улучшило качество поверхности и точности угла конуса.
Работая над кольцами Бриггса, я решил попробовать применить свой притир для доводки резьбовых калибров-пробок и, как только покончил с кольцом, эту идею осуществил.
Для измерения и периодического контроля среднего (основного) диаметра резьбы калибрового кольца необходимы контрольные калибры-пробки. Обычно такие калибры делались на резьбошлифовальных станках сразу в размер, и резьба на них не доводилась притирами. Эта неправильная технология сразу бросалась в глаза.
В самом деле, что получалось в результате такой технологии? Допуск по среднему диаметру резьбы контрольного резьбового калибра составляет всего 0,004-0,006 мм, «поймать» его резьбошлифовщику весьма трудно, поэтому много калибров шло в брак. Но и те, которые случайно получались в размере, были весьма низкого качества и очень недолговечны.
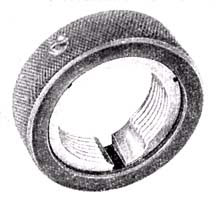
Притир для наружной резьбы контрольного калибра
Даже самый лучший резьбошлифовальный станок оставляет на профиле резьбы мельчайшую «дробь». Величина этих неровностей ничтожно мала — всего 1-2 микрона, но ведь это резьба! На одной плоскости резьбы бугорок в 1 микрон, на второй — 1 микрон, вот уже 2 микрона. Но калибр-то круглый! Значит, с другой стороны-тоже «дробь» в 2 микрона! Итого уже 4 микрона. А весь допуск — тоже 4 микрона!
Хорошо, если удалось попасть в верхний предел допуска, тогда калибр еще успеет проверить несколько калибровых колец, не выйдя из размера. А если попал в нижний допуск? Тогда при первом же свинчивании калибра с каленым кольцом эти микроскопические бугорки сразу «слетают», и контрольный калибр можно выбросить — он уже ниже допуска.
Массовое изготовление шлифованных контрольных калибров меня и удивляло и возмущало. Кроме того, подгонка калибрового кольца по шлифованному контрольному калибру — дело весьма затруднительное. Все эти мельчайшие бугорки «дроби», ничтожные погрешности шага, невидимые отклонения угла резьбы, некоторая эллипсность калибра, неизбежная даже при самом тщательном шлифовании резьбы, — все это нарушало плавность свинчивания. Понятно, как токари-лекальщики мучились с каждой партией резьбовых калибровых колец.
Допуск на резьбу самого калибрового кольца составляет 10-14 микрон, поэтому «запороть» кольцо по таким контрольным калибрам — весьма обычное дело.
Многочисленные опыты, отраженные в технической литературе, давно уже показали, что доведенные контрольные калибры, помимо ликвидации всех этих бед, имеют срок службы в 6 раз больший, чем шлифованные калибры, а стоят они только в 1,5 раза дороже шлифованных. Однако, когда я показал эту литературу мастерам и технологам цеха, они в один голос заявили, что все это хорошо только в книжках, а на деле ничего не выходит.
— Пробовали уже доводить контркалибры — ничего не вышло. Ну как ты доведешь калибры УНЕ, КНЕ, КИНЕ? — наступали они на меня. — У них площадка по наружному диаметру резьбы три — шесть сотых миллиметра! Нарежут ребята притир, он сядет на эту площадку и трет ее, а средний диаметр, тот, что надо доводить, и не трогает! По наружному диаметру калибр уже брак, а по среднему — еще доводить надо. Пробовали и бросили.
Моя идея была проста, как апельсин: то, что я сделал для получения внутренней резьбы колец Бриггса, надо сделать для наружной резьбы контрольных калибров. И я рискнул — пошел против технического отдела и против мастеров. Конечно, кое-кто стал смотреть на меня косо.
Я понимал, что изменить технологию будет трудно. Пошел к начальнику цеха Алексею Михайловичу Строеву. Сам в недавнем прошлом слесарь-лекальщик, Строев сразу понял идею, оценил ее выгоды и сказал:
— Контрольные калибры будем доводить твоим методом, а за нормаль резьбы Бриггса — спасибо! Где твое предложение?
Я сказал,что в техотделе. Через несколько дней Строев подошел к моему станку и сказал:
— Твоя технология утверждена вопреки протестам техотдела, а за предложение получишь 1000 рублей (это было еще по старым ценам) — оно признано техническим усовершенствованием.
Кроме Строева вряд ли кто в цехе понял тогда сущность полуходового притира, но выгода его была налицо.
Я заметил, что токари-лекальщики — старожилы завода — иногда подсматривают за мной, когда я нарезаю на станке новый притир, а потом собираются вместе и обсуждают — как же его нарезать? Воспитанные на старых традициях, они, видимо, ду мали, что я «зажму» секрет изготовления притира и один буду извлекать из этого какие-то выгоды. Поэтому они даже не пытались расспросить меня. Невольно вспомнился ленинградский завод «Пневматика», где я сам исподтишка подсматривал за работой отличнейших лекальщиков Зайко и Дмитриева и не решался ничего у них спросить, будучи уверен, что они все равно ничего мне не расскажут.
Но я не делал тайны из своего метода. Сперва показал, как надо нарезать новые притиры токарю А. Савину, потом токарю В. Максимову, потом В. Корытцеву. Они быстро освоили новые приемы и по сей день, при надобности, успешно пользуются ими. С 1952 г. все контрольные резьбовые калибры на нашем заводе выпускаются только с доведенной резьбой. Долговечность их возросла в 6 раз, и, естественно, требоваться их стало гораздо меньше.
В настоящее время притир с полуходовой резьбой известен токарям-лекальщикам многих заводов нашей страны.
Все время я был так занят новой техникой, что как-то не заметил, что стал «фигурой» в цехе. Меня выбрали в цеховой комитет профсоюза, года три я был заместителем председателя цехкома и вел производственный сектор. В то время у нас в цехе был замечательный секретарь партийного бюро Александр Сидорович Баранов. Он часто приходил к станку и подолгу беседовал со мной. Однажды он сказал мне:
— А почему ты, Борис Федорович, до сих пор не в партии?
Я шутя ответил:
— Поручителей нет!
А сам подумал: «А почему, в самом деле? И почему я об этом никогда не задумывался?»
Видимо, я так увлекся своей техникой, что на какое-то время забыл про все остальное.
Рекомендации в партию мне дали секретарь партбюро Баранов, начальник центральной измерительной лаборатории Фалеев и начальник цеха.
И вот настал день, когда меня приняли в кандидаты партии. А через год я был членом КПСС. Чувствуя за собой теперь большую ответственность, я старался работать еще лучше. Одному из первых на заводе мне вручили личное клеймо. Такое высокое доверие было, конечно, очень приятно.
Хочется сказать несколько слов о моих учениках. Всего их было, наверное, около сорока — люди совершенно различные, с разными характерами, мыслями, целями и стремлениями. Всем им я старался привить любовь к нашей трудной и интереснейшей профессии. Не все выдерживали тяжелую науку токаря-лекальщика, был и «отсев». В настоящее время рядом со мной работает только один мой ученик — Владимир Корытцев. Ученик- это только так говорится. Он имеет 5-й разряд новой тарифной сетки, зарабатывает 200 рублей в месяц, считается в цехе одним из главных «зубров» по резьбовым делам.
Остальные мои ученики, познав тайны токарно-лекального искусства, разбрелись по другим заводам. И я считаю, что это правильно и закономерно.
Вот, скажем, мой бывший ученик Сафиула Исхакович Нуриманов. Татарин по национальности, он с большим трудом закончил русскую школу, попал на наш завод и впился в токарно-лекальное дело, как клещ. Дело давалось трудно, одна неудача следовала за другой, но он не сдавался. Видя такое упорство, я проникся к нему уважением и решил во что бы то ни стало сделать из него настоящего лекальщика.
Пришел он ко мне уже квалифицированным токарем, а учился у меня целых три года вместо положенного одного. И все-таки он выучился и стал отличным токарем-лекальщиком. Сейчас он работает на московском машиностроительном заводе «Коммунар» и считается там главным «резьбовых дел мастером». Сафиула Исхакович добился своего.
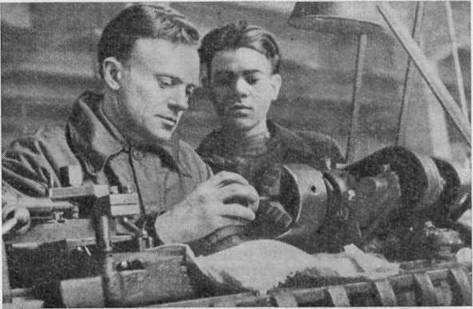
Сафиула Нуриманов (справа) не упустит ни одного движения
Другой мой ученик — Анатолий Пономарев — человек иного склада. Подвижный, веселый, он все делал как бы шутя и все ему удавалось с первого раза. Однако работа его полностью не удовлетворяла, и, еще не окончив учебу у меня, он поступил в вечерний институт. Пять лет он совмещал сложную работу с учебой и все же получил диплом с отличием. Сейчас он ведущий инженер одной из лабораторий ВНИИАлмаз.
И Нуриманов и Пономарев бывают у меня и теперь. Приходят они по разным вопросам, а цель одна — посоветоваться, получить консультацию.
Нуриманов обычно приходит, когда ему поручают новую, еще незнакомую работу. Получив консультацию, а то и соответствующий новый инструмент, он уходит довольный и через несколько дней звонит по телефону: все в порядке, спасибо.
Анатолий Пономарев занят исканиями. Иногда он приходит с такой идеей, на какую я и не замахивался. Такова, например, его идея изготовить твердосплавные плоские резьбовые плашки для накатывания резьбы на болтах. Идея сулит огромные выгоды, такого инструмента еще нет в Европе, а вот мой ученик Анатолий Пономарев уже сделал такой инструмент и удивляет им специалистов!
Была еще у меня ученица Людмила Ходова, или, как ее все звали в цехе, Мила. Эта худенькая блондиночка несколько лет работала токарем. Имела законченное среднее образование и училась в заочном институте. По-моему, успешно учиться в заочном институте могут только одаренные и волевые люди. У Милы волевой и сильный характер. Она довольно быстро освоила доводку резьбовых контрольных калибров — операцию, которая не давалась многим квалифицированным токарям-мужчинам. Пять лет она проработала рядом со мной, сперва ученицей, а потом самостоятельно, и всегда была энергична и весела, несмотря на трудную и напряженную учебу.
Она блестяще защитила дипломный проект и ушла из цеха. Сейчас работает инженером-программистом, составляет программы и задания для станков с программным управлением. Дело это новое и, признаюсь, для меня малопонятное. При каждой встрече Мила пытается подробно объяснить мне сущность электронно-вычислительной системы программного управления. Она, как и раньше, увлечена своей работой, всегда такая же быстрая и энергичная. Людмила — коммунистка, избрана членом парткома завода.
Я мог бы назвать не один десяток учеников — у каждого своя судьба, своя дорога в жизни, но большинство все-таки работают сейчас на заводах Москвы и других городов по профессии токаря-лекальщика.
Вернемся к моей общественной работе. В 1953 г. трудящиеся Ленинградского района избрали меня своим депутатом, а в 1955 г. я был избран членом исполкома Ленинградского райсовета.
Помню, как один из секретарей райкома — т. Косовский спросил: «Какую работу хотели бы вести как депутат?» Я ответил: «Что-нибудь связанное с техникой». Косовский засмеялся и сказал, что общественной работы, связанной с техникой, пока нет, придется заняться другой.
Несколько лет я, как депутат, контролировал жилищное строительство в районе, наблюдал, по мере своих возможностей, за правильностью распределения жилой площади.
Дел было много, но рационализацию, новую технику я не бросал — они вошли в мою жизнь прочно, навсегда.
Тогда я не подозревал, что недалеко время, когда общественная работа в области новой техники, в области’ новаторства захватит крепко многих рабочих нашего времени.
Больше книг — больше знаний!
Заберите 20% скидку на все книги Литрес с нашим промокодом
ПОЛУЧИТЬ СКИДКУ