Рождение железного века
Рождение железного века
Сорок тысяч тонн. Три с половиной миллиона тонн. Десять миллионов тонн.
Эти цифры — этапы развития английской металлургии.
Сорок тысяч тонн чугуна дала Англия в 1780 году.
Три с половиной миллиона тонн чугуна выплавили доменные печи Великобритании в 1856 году.
В три раза больше дали они через полстолетия — десять миллионов тонн в 1913 году, когда шли последние лихорадочные приготовления к мировой схватке — почти предел, достигнутый английской металлургией (мощность домен в 1913 году — 11 миллионов тонн, мощность их в 1927 году — 12 миллионов тонн).
Три с половиной миллиона тонн выплавлено было еще через двадцать лет — в 1932 году, когда кризис остановил многие десятки домен Англии.
Годы юности, цветущей зрелости, увядания, дряхлой старости отражены в этих цифрах.
Из слушателей Бессемера едва ли кто-нибудь мог бы себе представить, что таков будет итог семидесятипятилетнего развития английской металлургии. Если бы кто-нибудь сказал, что английская металлургия через 75 лет снова вернется на ту же самую точку, то конечно никто из присутствующих не поверил бы этому, хотя им самим и их отцам довелось увидеть гораздо более удивительные вещи. Вероятно большинство слушателей Бессемера знало, что лет восемьдесят назад, в 1775 году, все домны Соединенного королевства, из которых многие еще дожигали последние остатки замечательных дубовых рощ, дали тогда всего только 32 тысячи тонн чугуна в год.
Тридцать две тысячи тонн в год это столько, сколько в 1934 году дает СССР в один день, столько сколько дает в один месяц одна домна Магнитогорска.
Но и среди слушателей Бессемера набрался бы пожалуй десяток-другой заводчиков, из которых каждый мог бы сказать, что его завод выплавляет чугуна в год побольше 30 тысяч тонн.
И действительно огромен подъем британской металлургии за это восьмидесятилетие (1770–1850 годы). В сто раз почти увеличилась ее продукция. Вот те неровные ступени, по которым происходит этот подъем (в тысячах тонн выплавленного в год чугуна):
Годы
1770……32
1780……40
1790……80
1800…….156
1806……258
1823……452
1830……678
1840…..1396
1848…..1998
1852…..2700
1856…..3528
Но эти цифры — лишь вехи того огромного сдвига, который известен под названием промышленной революции, до неузнаваемости изменившей и технику и строй промышленности и общественные отношения не только Англии, но и других стран.
Машина вытесняет человеческий труд. Механизм вырывает орудие, инструмент, из руки работника и выполняет его работу. Новая сила природы порабощается на службу производства — сила пара. Распадаются тесные рамки прежнего мануфактурного «рукодельного» производства, ограниченного человеческими пределами «силы, ловкости, искусства рабочего». Ничто теперь не мешает производить все больше и больше, — производить, чтобы получать прибыль и снова производить товар, но уже в большем количестве и снова получать прибыль, тоже большую. И растущий и крепнущий с каждым часом капитал в силу органически ему присущей безграничной жажды «расширенного воспроизводства» выбрасывает все новые и новые груды товаров, обрушивающиеся иногда на него тяжелыми лавинами кризисов. И ничто не мешает извлекать все большие и большие количества добавочного человеческого труда. Ведь мастерская ремесленника с двумя-тремя работниками превратилась в фабрику-завод со многими сотнями обезличенных «рук» (таково на предпринимательском языке название рабочего), в которые превратились прежние искусные мастера. Эти «руки» легко заменимы и потому обесценены: ведь за воротами фабрики всегда стоит и ждет работы голодающая резервная армия обезземеленных крестьян и разоренных ремесленников.
Средство производства начинает занимать в промышленности все большее и большее место, а вместе с этим создается и приобретает все большее значение и новая отрасль промышленности: производство средств производства.
Далее, «революция в способе производства промышленности и земледелия делает необходимой революцию в общих условиях общественного производственного процесса, т. е. в средствах сношений и транспорта» (Маркс «Капитал», т. I).
Во всех этих сдвигах черный металл сыграл громадную роль. Коротко говоря, он явился тем материалом, из которого капитализм создал свою систему орудий производства. Понятно, что сильные изменения должны были произойти в способах применения металла и в способах его производства и обработки.
Цифры продукции чугуна говорят о возрастании спроса на черный металл, о совершенно новых и широких областях применения его. Это не значит, что исчезли и старые области его применения и потребления. Но они оттеснены далеко на второй план.
На что шел металл в половине XVIII столетия, скажем в шестидесятые годы, накануне введения паровой машины, в годы крупных изобретений в текстильной технике, в годы зарождения машинного производства? На что идет он в половине XIX века? Мало схожих черт найдется в потреблении и применении металла в эти два момента.
Металлургия — один из самых широких и рано открытых путей вторжения торгового капитала в производство. Металлургическое производство одно из первых, во всяком случае не позже хлопчатобумажного, приняло капиталистические формы. Железозаводчиков, владевших большими предприятиями, можно встретить уже тогда, когда и крупные «мануфактуристы» текстильщики насчитывались немногими единицами.
Некий Вильям Вуд в первой половине XVIII века держал в аренде все королевские рудники, имел несколько доменных печей. Что производил он? «Горшки, полосы, перила, плиты для очагов и каминов и всякий другой литой чугунный товар». Вот что отливал он из своих домен.
В конце пятидесятых годов XVIII века был основан металлургический завод в Карроне в Шотландии, скоро ставший одним из крупнейших предприятий: уже в шестидесятых годах на заводе работало (повидимому вместе с принадлежащими ему каменноугольными копями) 800 человек.
Что же производит карроновский завод? «Тут производится, — пишет один путешественник, — огромное количество горшков, котлов для сахароварения, пушки и всякий другой чугунный товар. Много пушек отправляется в Испанию». Чугунные пушки завода, знаменитые «карронады», славились на всю Европу.
Самым крупным потребителем металла в XVIII веке безусловно была артиллерия — в Англии главным образом морская. Пушками были вооружены не только военные, но и купеческие корабли.
Тяжелая 36-фунтовая (то есть стреляющая ядром, весом в 36 фунтов), чугунная пушка являлась пожалуй одной из самых крупных отливок. В 1795 году на английскую артиллерию чугунного литья ушло свыше 16 тысяч тонн: 11 тысяч для Великобритании и 5–6 тысяч тонн для Индии. За границу было вывезено 10 тысяч тонн. Карроновский завод был крупнейшим артиллерийским заводом.
Флот был самым крупным потребителем ковкого железа, в виде цепей и якорей. Якорь большого корабля являлся пожалуй самым большим предметом, сделанным из железа. На каждые 20 тонн водоизмещения корабля считали по 1 центнеру веса якоря, то есть для корабля в 1500 тонн нужен был якорь весом около четырех с половиной тонн.
Большое сравнительно количество железа шло на производство ружей. Этим издавна уже славились кузнецы большого села Бирмингэма. После «славной» революции 1688 года правительство стало заказывать им крупные партии оружия. Несколько позже, помимо отечественного рынка, эти ружья тысячами пошли в Турцию и бирмингэмское изделие не совсем безуспешно стало защищать султана против налетов «екатерининских орлов», стремящихся водрузить крест на святую Софию.
Бирмингэмское ружье вооружает марокканских, берберийских пиратов, которые ведь всегда очень охотно устроят небольшую диверсию против врагов старой Англии, или пограбят корабли нежелательных конкурентов. Но самым может быть выгодным был сбыт ружей в Африку, в Гвинею. Гвинея хорошо платила живыми крепкими неграми, которые так нужны были плантаторам в Америке. К тому же нечего было опасаться, что черное население будет вооружено современным оружием: ружья изготовлялись такого качества, что разрывались на первом же десятке выстрелов.
Очень трудно учесть, сколько железа уходило на изготовление жести (в пятидесятых годах XVIII века в Великобритании было четыре жестепрокатных завода), обручного, полосового железа, проволоки, гвоздей.
Сталь шла исключительно на изготовление инструмента, холодного оружия и галантерейного товара — иголок, пряжек и пуговиц. Блестящая стальная полированная пряжа и пуговицы к концу XVIII века кормили в Бирмингэме больше 20 тысяч человек. Знаменитый Болтон, покровитель и помощник Уатта, построил в шестидесятых годах свой огромный по тому времени завод в Сохо около Бирмингэма именно для производства пряжек, пуговиц, стальных цепочек.
Шеффильд славился своими напильниками и ножевым товаром.
Вот приблизительно и все виды применения черного металла: чугуна, железа, стали в XVIII веке.
Но не пропущено ли тут самого главного — металлической машины. Нет, не пропущено: таковой тогда еще не существовало. Металл и машина в нашем представлении сливаются в одно неразрывное целое, но еще в первые десятилетия XIX столетия видное место в машиностроении занимало дерево. Одному из создателей машиностроительной техники, Джемсу Нэсмиту, пришлось в юности, примерно еще в двадцатых годах XIX века, видеть деревянное оборудование металлургического завода. Оно оставило у него неизгладимое впечатление. Это были как раз знаменитые карроновские заводы. «Большая часть оборудования, — пишет Нэсмит, — была еще деревянной. Оно вообще говоря было еще вполне годным, но чудовищно громоздким. Оно производило впечатление огромной мощи и способности к сопротивлению, но в действительности оно таковым не было. Во всяком случае на непривычного человека оно производило подавляющее впечатление. Мастерская, освещаемая по временам добела раскаленными массами металла, с лучами солнца, пробивающимися только через немногие отверстия в крыше под темные закопченные дымные своды, под которыми в отдалении слышалось скрипение громоздких машин, тогда как движущиеся части лишь смутно виднелись в дымном воздухе, шипение выпускаемого пара и плеск воды, полуобнаженные рабочие, надрывающиеся около масс раскаленного железа и ковшей, наполненных расплавленным чугуном, — все это производило огромное впечатление на посетителя».
Там, где еще действовало водяное колесо, а оно далеко не везде еще было вытеснено паровой машиной, оно еще часто было сделано из дерева. И нередко инженер того времени, подбирая для него ось, доверял больше давно уже испытанной добротности старого дуба, нежели чугунной отливке ненадежного качества.
Одним из первых, который ввел чугун в машиностроение, был замечательный техник XVIII века — Смитон. Вот что писал он о своих первых шагах в этом направлении. «Когда я двадцать семь лет тому назад (то есть в 1755 году) впервые стал применять чугун, то все удивлялись, как может хрупкий чугун выдерживать там, где не может устоять самое крепкое дерево. Однако эти отливки несут свою службу исправно и по сию пору».
Черный металл пришел в машиностроение, поскольку таковое в XVIII веке существовало, вместе с паром. Большой, отлитый из чугуна цилиндр (как раз такие цилиндры и делались на карроновских заводах) атмосферной машины был первой крупной деталью из черного металла в машиностроении (котел делался обыкновенно из меди).
Но не следует преувеличивать значения на первых порах машиностроения, как потребителя черного металла.
К 1800 году в Великобритании было всего 320 паровых машин. Если считать, что они были построены за последние двадцать пять лет (с 1775 года), то на них в среднем ушло не больше нескольких сот тонн металла в год.
С каждым годом однако машиностроение будет поглощать все большие и большие количества металла. Но к концу XVIII века наметились еще и другие виды его применения.
В 1779 году «железные короли» Стаффордшира, Вилькинсон и Дерби, строят первый чугунный мост.
В 1787 году Вилькинсон спускает первое железное судно — небольшую речную шаланду тонн в двадцать.
В 1788 году он отливает по заказу Парижа сорок миль водопроводных чугунных труб.
Чугун и железо идут как строительный материал. На заводе Болтона и Уатта в Сохо некоторые мастерские были построены частью из металла: чугунные лестницы, полы, стропила.
Оборудование металлургических заводов становится более тяжелым. В первые годы XIX века некоторые молота весили до 10 тонн, прокатные валы — 16–24 тонны, маховые колеса — 9 тонн.
Наступает XIX век, и с каждым годом возрастают все эти виды потребления металла, лишь наметившиеся в предыдущем столетии.
Как ни велико значение постройки паровой машины для развития технологии металла, однако не следует преувеличивать значение машиностроения как потребителя металла. В конце концов все это потребление металла машиностроением исчисляется несколькими десятками тысяч тонн в год. Еще в большей мере можно сказать то же самое про пароходостроение и железное судостроение.
В половине XIX века на пароходные машины уходило не больше 1–2 тысяч тонн металла в год, а железные суда были еще столь редки, что для них даже не были выработаны технические условия, которым они должны были удовлетворять.
Всепожирающий молох металла вырос на суше. Это — железная дорога. Железный, а первоначально чугунный, рельс имеет довольно длинную историю еще до того времени, когда по нему пошел первый паровоз.
Технический директор и пайщик Кольбрукдэльского завода, Рейнольдс, первый в 1767 году заменил деревянные брусья, по которым ходили тележки, подвозящие руду и уголь, положенными на бревна чугунными пластинами с неглубоким, плоским жолобом на верхней поверхности, которые и направляли колесо тележки. В 1793 году Утрам (может быть отсюда «дорога Утрама» — Трама — происходит слово трамвай) снабдил эти чугунные, длиною в один метр, пластины снизу ребром, которые служили для прикрепления рельса.
Уже эти чугунные рельсы, быстро распространившиеся по рудникам и металлургическим заводам, значительно увеличили спрос на чугун.
В 1803 году был выкатан первый рельс из сварочного железа.
Но днем рождения железнодорожного транспорта следует считать день 14 июня 1830 года, день победы Стефенсоновской «Ракеты» на конкурсе паровозов на Ливерпуль-Манчестерской железной дороге.
Появился новый и очень жадный потребитель железа.
Это может быть лучше всего поняли противники железной дороги: ведь среди многочисленных аргументов, приводимых ими против этого гибельного новшества, фигурировала и угроза, что железные дороги потребуют так много железа, что его цена возрастет вдвое, что железопромышленность не в состоянии будет даже вообще удовлетворить спрос, что неизбежно наступит полное истощение этого металла. Конечно, эти мрачные предсказания не сбылись, но железо действительно скоро потребовалось в очень большом и все возрастающем количестве.
В конце сороковых годов считали, что на изготовление всех необходимых изделий, как железных, так и чугунных, на одну милю железнодорожного пути: рельсы, стрелки, мосты, прокладки и т. д., а также подвижной состав, должно было затрачиваться около 700 тонн чугуна, из которых большая часть — около двух третей — должна была быть переработана в ковкое железо. А текущий расход металла, как сообщали русские инженеры, в Англии считали 40–50 тонн железа в год на одну милю.
В 1830 году в Англии было всего 86 миль железных дорог. В 1840 году их стало почти в десять раз больше — 836 миль, а к концу 1850 года железнодорожная сеть возросла до 6,5 тысяч миль, то есть в 80 раз против 1830 года.
На ряду с этим сильно увеличивается и вывоз металла. Ведь из английского материала строятся железные дороги, начинающие покрывать континентальную Европу и Новый Свет.
В общем можно считать, что великобританская металлургия, которая в середине пятидесятых годов давала больше половины (51,5 %) всей мировой выработки чугуна, вывозила около половины всей своей продукции главным образом в виде сварочного железа. Львиная доля в этом вывозе приходилась на железнодорожный инвентарь, главным образом рельсы.
Какими же техническими средствами удовлетворялся этот, все возрастающий спрос на черный металл, как росли орудия производства и развивалась его организация?
Архивы английских заводов могли бы дать, вероятно, на все это исчерпывающие ответы, но немногие из них уцелели и эти уцелевшие еще ждут своих исследователей.
Но для истории английской металлургической техники и экономики найдутся и другие источники, руководители и проводники.
Этими проводниками будут те иностранные и английские инженеры, техники, иногда просто путешественники, которые оставили нам описания и заметки о промышленности Великобритании.
Картины английской металлургической техники и промышленности, набросанные в разные хронологические моменты ее развития, выяснят нам и происшедшие в ней сдвиги.
Европейские специалисты горного дела и металлургии присматривались к английской технике уже тогда, когда Англия еще не была «мастерской мира». Швед Сведенборг, замечательный геолог и металлург, под старость свихнувшийся в мистику и богоискательство, объезжал Англию еще в тридцатых годах XVIII столетия и дал описание тогдашней английской горной и металлургической техники.
В шестидесятых годах XVIII века важнейшие металлургические и горные районы Англии осмотрел молодой талантливый французский геолог Габриэль Жар.
На рубеже XIX века, когда всем стал ясен тот огромный скачок вперед, который сделала английская металлургия, когда все увидели, насколько далеко она ушла вперед против континентальной Европы, Англия возбуждает особенно большое любопытство в техническом мире Европы. Изо всех стран едут инженеры знакомиться с новыми достижениями английской техники. Тут и швед Сведенштерна из страны бесподобного железа, с которым может конкурировать только уральский металл, тут и немец Фишер из страны, металлургия которой хоть и поотстала сейчас (то есть в годы его поездки) от английской, но история которой имеет такие блестящие страницы в прошлом и скоро даст замечательных теоретиков металлургов. С жадным любопытством всматриваются в успехи далеко ушедшей вперед соперницы французские инженеры Бонар и Фожа де Сен-Фон.
В тридцатые, сороковые, пятидесятые годы XIX века по английским заводам нас поведут русские инженеры — Корпуса горных инженеров майоры, полковники, капитаны. О них стоит сказать два слова.
Николаевское правительство внимательно следило за развитием и успехами английской промышленности. Качество пушки и ядра, ружейного ствола и сабли все тяжелее и тяжелее ложилось на весы международной политики. «Великой державе» нельзя было отставать от своих западных соперников.
Даже и в отсталой крепостной Российской империи с ее огромными пространствами все более и более назревала необходимость строить, хотя бы через силу, новые пути сообщения — железные дороги. На первых порах приходилось все заказывать заграницей и в первую очередь в Англии. Впрочем тут русские делали то же самое, что и другие государства западной Европы и Америка. Но делались также энергичные попытки наладить собственное производство.
Выросшая в необозримых лесах на чистом древесном топливе, на замечательных рудах и на даровом крепостном труде уральская металлургия, широко позаимствовав иностранный, главным образом шведский и английский, опыт, в конце XVIII века заняла одно из первых мест в Европе. Она сохранила его и в начале XIX века, но без непрерывного усвоения и в дальнейшем западно-европейской, в частности, английской техники удерживаться на прежнем уровне становилось все более и более затруднительным, особенно когда технические усовершенствования стали следовать друг за другом все более и более быстрым темпом.
Некоторые вновь возникшие отрасли производства были совершенно неизвестны в России. Это было понятно даже правительству Николая I, и мы видим, что, несмотря на всю ненависть к революционному западу, потрясающему «устои», оно что ни год командирует в Англию, да и не в одну Англию, инженеров и военных для осмотра заводов, для знакомства с производством. Характерно, что не столько самое получение черного металла, выплавка чугуна, сколько дальнейшая его переработка в железо и сталь и выработка изделий, главным образом массовых полуфабрикатов: процессы пудлингования и прокатки, в частности, изготовление рельс, является предметом особенного внимания русских металлургов.
Некоторые из этих русских техников производили очень хорошее впечатление на англичан, как люди толковые и знающие.
«Мне часто приходилось встречать, — пишет один из выдающихся машиностроителей Англии того времени, Джемс Нэсмит, — русских военных и инженеров. Обыкновенно это были люди очень способные, выбранные русским правительством в качестве его агентов за границей, чтобы держать его в курсе всего того, что представляет для него какой-нибудь интерес. Они несомненно создавали самую высокую репутацию своему правительству, являясь живым доказательством того, как тщательно выбирало оно лучших людей, чтобы поддерживать интересы России».
Впрочем, Нэсмит имел все основания быть довольным русским правительством и его представителями за границей. Он дружил с адмиралом Корниловым, удостаивался посещений «высочайших особ» (великого князя Константина), а главное он был завален русскими заказами. Нэсмит охотно пускал осматривать свой завод — это было своего рода рекламой и одним из способов получить заказ. Однако один раз он чуть было не поплатился очень жестоко за это. Важнейшее его изобретение — паровой молот — чуть было не ушло в чужие руки. Представители французского завода Крезо во время одного из посещений завода Нэсмита в его отсутствие внимательно рассмотрели и срисовали показанные им эскизы еще не запатентованного парового молота, построили его у себя и запатентовали на свое имя во Франции.
Далеко впрочем не все заводчики отличались таким либерализмом, как Нэсмит. Нередко любопытствующим посетителям приходилось наталкиваться на вполне резонное нежелание заводчиков раскрывать свои производственные секреты, выслушивать заявления, что «высматривать устройство они никому не позволяют», мириться с обходом завода «с величайшей поспешностью» иногда в сопровождении «ничего непонимающего в производстве конторского писаря». О зарисовках, измерениях, записях на месте конечно не могло быть и речи. На все это жаловались русские инженеры в своих отчетах.
Чтобы разузнать нужные и интересные вещи необходимо было проявить и кое-какие способности к соглядатайству. Русские в этом отношении оказались довольно талантливыми. Капитан Якоби для пользы дела не погнушался свести дружбу с людьми и низшего звания. Когда официальное обращение к владельцу завода с просьбой сообщить некоторые сведения и чертежи не увенчалось успехом, то предприимчивый капитан, — как пишет он в своем отчете, — «счел за нужное поселиться по близости самого завода, чтобы, сблизясь с г. Бойделем (одним из владельцев завода), его мастерами, письмоводителями и чертежником, завести с ними теснейшее знакомство и приобрести дружбой то, что нельзя было приобрести за деньги. В какой мере оказался расчет мой, — пишет он, — верным, объяснится ниже». А расчет действительно оказался верным, и «ниже» было представлено подробное, на полусотне страниц, с цифровыми данными описание завода и наиболее интересных технологических процессов.
Итак начнем наш путь, и глазами современников посмотрим, как строится и как работает эта «мастерская мира», или по крайней мере некоторые ее пролеты, те именно, где производится самый материал, из которого капиталистическая техника создает и будет создавать самые орудия производства — черный металл.
Отвлечемся только от наших современных масштабов и будем мерить не меркой будущего, но скорее шагами уже пройденного пути и тогда мы с уважением посмотрим на «огромные» для людей восьмисотых или сороковых годов крохотные для нашего времени, доменные печи и заводы, талантливыми и искусными способами должны мы будем признать способы и методы работы и нечеловеческим затрачиваемый труд, сугубо бесчеловечной эксплоатацию.
Словами изящной лести начинается предисловие к одному французскому металлургическому трактату XVIII века.
«Просвещенный министр, который для своих патриотических планов привлекает все, что может увеличить мощь и силу государства, признал важность горного дела в наш век и сознал необходимость содействовать развитию национальной металлургии… Но в том убеждении, что одна только теория, без умения приложить ее к практике, является бесполезным умствованием, он развил дальше свои цели. Тот же дух, который побудил его отправить философов в отдаленные страны, чтобы определить фигуру земли, внушил ему, что путешествие явится лучшим способом обучения и доведения до совершенства искусства добывать и обрабатывать металлы, зарытые в недрах земли».
Выбор просвещенного министра Франции пал на молодого минеролога и металлурга, Габриэля Жара, и оказался чрезвычайно удачным. В 1757 году двадцатипятилетний Жар отправляется в свою первую научную командировку в Германию и Венгрию. Через несколько лет, в 1765 году объезжает он Англию и Шотландию, а в следующем году знакомится с горным и металлургическим делом в Северной Германии, Швеции и Норвегии.
Блестящие отчеты его о своих наблюдениях в этих краях дали ему звание академика, но ранняя смерть — он умер 37 лет от роду — помешала ему свои путевые записки литературно обработать. Его брат выпустил их в виде книги «Металлургические путешествия, или исследования и наблюдения о железных рудниках, о кузницах (металлургических заводах), об изготовлении стали, жести и о шахтах земляного угля, произведенные с 1757–1769 гг. в Германии, Швеции, Норвегии, Англии и Шотландии». Книга эта явилась одним из превосходных пособий по металлургии XVIII столетия. Отрывок из ее предисловия мы только что процитировали.
Что же увидел Жар в Англии?
Жар начал свое обозрение с северной Англии, с Нью-Кэстля, проехал затем на западное побережье в Кумберланд, откуда перебрался в Ланкашир и затем в старинный металлургический район Стаффордшир. Путешествие он закончил проездом через Шеффильд и обозрением Шотландских заводов. Им были, таким образом, осмотрены почти все районы, в которых процветала и в будущем особенно пышно развилась английская металлургическая промышленность. Это можно сказать классический маршрут технических паломничеств в Англию.
Жар приехал в Англию на заре нового железного века в технике, когда английская металлургия делала первые шаги по тому пути, который привел ее к изумительному расцвету. Тогда только что, да и то еще довольно слабо, начинали сказываться результаты первой победы в борьбе за новое топливо, которую вот уже больше столетия вела английская металлургия и которая продолжится до самого конца XVIII века.
Когда многочисленные маленькие, но прожорливые домны Южной Англии дожигали остатки дубовых лесов, молодой владелец литейного завода на быстром горном ручье Кольдбруке в отдаленном лесистом еще Шропшайре — на западе Англии, Абрагам Дерби, продолжая работу своего отца, железных дел мастера и заводчика, тоже Абрагама Дерби, получил первый чугун, выплавленный не на древесном угле, а на коксе. Многолетние труды увенчались успехом. Это случилось в 1735 году. Сын Абрагама Дерби тоже Абрагам, третий по счету, внес некоторые улучшения. В результате этой работы трех поколений, черная металлургия Англии не только вышла из того тупика, куда грозило завести ее уменьшение, местами полное исчезновение ее топливной базы — вырубка лесов, но перед ней открылись и новые широкие горизонты. Теперь оказывалось возможным использовать те втуне до сих пор лежавшие сказочные богатства каменного угля и руды, которыми владела страна. 1735 год — знаменательный год, но не только в истории английской металлургии и английского хозяйства: в этом году был заложен один из краеугольных камней всей дальнейшей капиталистической техники и промышленности.
Плавка на коксе начинает распространяться в Англии с конца сороковых годов XVIII века. До этого она почти совершенно не была известна за пределами Кольбрукдэля, — так стал называться небольшой городок, в который превратился завод Дерби на ручье Кольдбруке. Он будет расти и скоро станет важнейшим рассадником металлургической техники.
Для француза Жара плавка на коксе была крупнейшей технической новинкой, открывающей возможности производства чугуна в неограниченных размерах. Но Жар подсмотрел и описал еще и другую новинку — способ производства самого высококачественного вида литого металла — тигельную сталь. Трудно себе представить, как удалось ему выведать тайну этого производства, которую так ревниво охраняли шеффильдские фабриканты, сами, впрочем, выкравшие ее у изобретателя, часовщика Бенжамена Гэнтсмана. Гэнтсман открыл этот способ получения стали около 1740 года, то есть за 25 лет до приезда Жара, однако именно Жар дал нам первое описание этого производства. Его рассказ стоит прослушать, ведь техника выработки тигельной стали осталась почти неизменной не только до времен Бессемера, но и почти до нашего времени.
Изготовление тигельной стали, как известно, распадается на две стадии: первая — это так называемая цементация и затем переплавка этой цементной стали в тиглях.
Первая стадия — цементация, то есть пропитывание углеродом полос мягкого железа, была известна в Англии уже давно. Родина этого способа — центральная Европа, в особенности Австрия. На этой стадии собственно и заканчивался процесс передела железа в сталь, которая дальше шла на изготовление всевозможных изделий. В Англии цементную сталь делали только в Нью-Кэстле и Шеффильде. Переплавка стали в тиглях и явилась тем новым, недавно сделанным изобретением, которое значительно улучшало качество продукта, делало его более однородным.
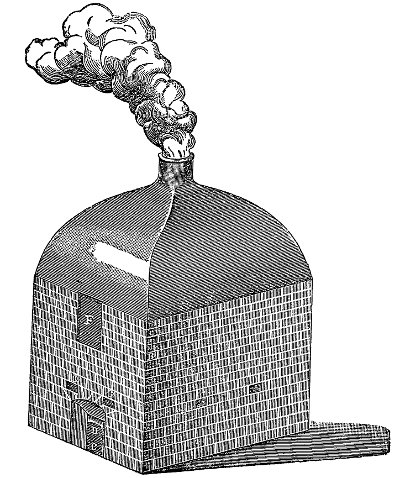
Печь для выработки цементной стали 60-х годов XVIII века. 1. Наружный вид
«Печи для приготовления стали около Нью-Кэстля, — пишет Жар, — различной величины, но построены они на основании одних и тех же принципов. Внешнее каменное строение представляет собой продолговатый прямоугольник. Внутри его посередине, в длину сделана чугунная решотка, лежащая горизонтально на уровне пола. Шириною она в 20 дюймов, под ней находится поддувало. Над решоткой приблизительно на высоте 16 дм. находится место, на котором расположены ящики, в которые кладется обрабатываемое железо. С каждой стороны устроено по десяти горизонтальных дымоходов, на них из огнеупорного песчаника выведены ящики и швы замазаны глиной. Внутри ящики длиною в 10 1/2 футов, шириною — в 2 фута 4 дюйма и глубиною в 2 фута 6 дюймов. Пламя охватывает их со всех сторон.
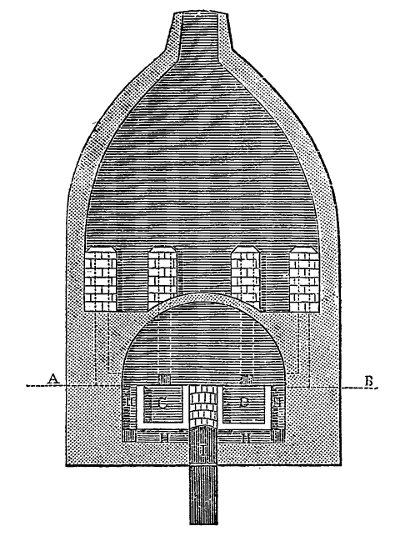
Печь для выработки цементной стали 2. Вертикальный разрез по короткой стороне. C и D — калильные или цементационные ящики; H — каналы, по которым проходит пламя; I — топочное пространство.
С боков ящики укрепляются перемычками и так прочно, что выдерживают и вес загруженного в них железа и действие пламени. Над этими ящиками и всем внутренним пространством печи выведен купол, который удерживает жар, а дым и пламя выходят через восемь дымоходов. Вся печь стоит под дымовой трубой, выложенной из кирпича, в виде сахарной головы. Одно только шведское железо признается годным для превращения в сталь. Было произведено много опытов и с английским железом, но из него никогда не могли получить столь же добротной стали, как из шведского…
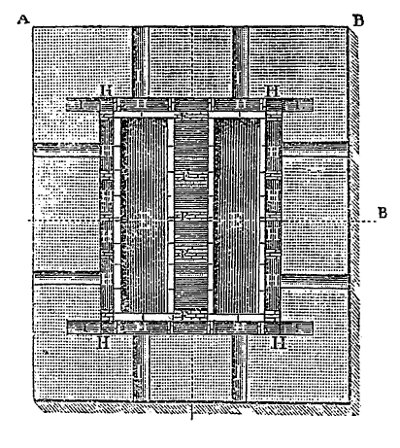
Печь для выработки цементной стали 3. Горизонтальный разрез по линии A — B. E — цементационные ящики; F — перемычки; H — каналы, по которым проходит пламя.
Для загрузки печи мастер заползает внутрь и ему туда подаются через отверстия в стенках полосы. Мастер насыпает на дно ящика слой толченого и просеянного через решето древесного угля, немного смачивает его и кладет ряд железных полос. На них снова насыпается слой угольного порошка, толщиною 1 дюйм, на него снова кладется ряд полос, и так продолжают, пока ящик не будет наполнен доверху. Верхний ряд полос засыпают слоем угля, и затем насыпают слой песку для того, чтобы горючее вещество в ящике лежало бы плотнее и не превратилось бы в пепел от действия жара. Употребляют мокрый песок, смачивая его, когда он высыхает. Песок накладывается более толстым слоем к середине, так что тут он имеет около 10 дюймов толщины. Заложив железо в ящики, закрывают все отверстия и зажигают печь.
Обыкновенно печь зажигают в понедельник вечером и поддерживают сильный огонь до субботы. После пяти дней и ночей непрерывного нагрева, когда, полагают, железо целиком превратилось в сталь, выламывают каменную кладку, которой были заложены отверстия, раскрывают заслонки, сбрасывают уголь с колосников в зольник, чтобы остудить печь. Нужно ждать еще целую неделю, пока сталь совершенно не остынет. До этого ее никогда не вынимают. Мастер, который закладывал железо, заползает тогда в печь и подает полосы другому рабочему.
Для этой работы нужно только двух рабочих, из которых каждый получает по 4 шиллинга за тонну стали. Эта сталь, когда она выходит из печи, называется пузыристой сталью. В таком виде она мало идет на продажу и центнер (1/20 тонны) стоит 26–28 шиллингов. Ее обычно проковывают еще под молотом и вытягивают в полосы толщиною в 7–8 линий и остужают ее на воздухе. Цель этой работы — придание ей большей плотности. Такая сталь называется обыкновенной сталью и ее употребляют для изготовления напильников, пил, ножниц, ножей и т. д. Ее много отсылают в другие английские провинции, в особенности Шеффильд и Бирмингэм. Центнер ее стоит 30–32 шиллинга».
Полученная таким путем цементная сталь и служила сырьем для выработки тигельной стали.
«При помощи следующей операции, — пишет Жар, — цементованная сталь еще больше рафинируется. Для этой цели употребляют всевозможные отбросы стальных изделий[7].
Пользуются печами, которые врыты в землю и имеют подвод воздуха под землей. У устья печи (в горизонтальной верхней крышке ее), лежащей вровень с полом, находится отверстие канала, идущего горизонтально к стене, от которой подымается труба. В этой печи можно поместить только один тигель, вышиною 9—10 дюймов и шириною в 6–7 дюймов. В него накладывается сталь с флюсом, состав его держат в секрете.
Тигель ставят на круглый кирпич, лежащий на решотке, затем вокруг тигля насыпают кокс и заполняют им всю печь. Зажигают огонь и закрывают верхнее отверстие печи заслонкой из кирпичей, стянутых железным обручем так, что пламя тогда идет по горизонтальному каналу в трубу. Тигель должен стоять пять часов в печи, прежде чем сталь совершенно расплавится. Затем она выливается в четырехугольные формы из чугуна (так называемые изложницы), состоящие из двух половин, накладываемых одна на другую. Вливание производится с одного конца.
Я видел слитки такой стали, они похожи на чугун. Сталь эта проковывается, как и цементная, под молотом, только ее следует нагревать слабее и с большей осторожностью, иначе она легко может лопнуть. Цель такой обработки — привести стальные частицы в более близкое соприкосновение друг с другом так, чтобы у нее не было «гнилых» пятен как у немецкой стали. Уверяют, что это достигается только от переплавки. Сталь эта употребляется не очень часто и только для таких изделий, которые требуют очень хорошей полировки. Из нее изготовляются лучшие бритвы, различные перочинные ножи, лучшие стальные цепочки, часовые пружины и маленькие напильники для часовщиков».
Так делали сталь в Англии в шестидесятых годах XVIII века. Таким же способом продолжали делать ее и в половине XIX века, но тогда, в шестидесятых годах XVIII столетия, это производство тигельной стали было замечательной технической новинкой, теперь же, ко времени Бессемера, оно превратилось в пережиток старого мануфактурного способа производства. Это был один из тех участков металлургической техники, где механизм еще не вытеснил руки человека, а из этого вытекали и все типичные для мануфактурного продукта черты, прежде всего количественная ограниченность производства, а отсюда и ограниченность его употребления. Бессемер ведь как раз первоначально и ставил себе задачу получения металла, который заменял бы тигельную сталь, но мог бы вырабатываться в больших количествах и более дешевым способом.
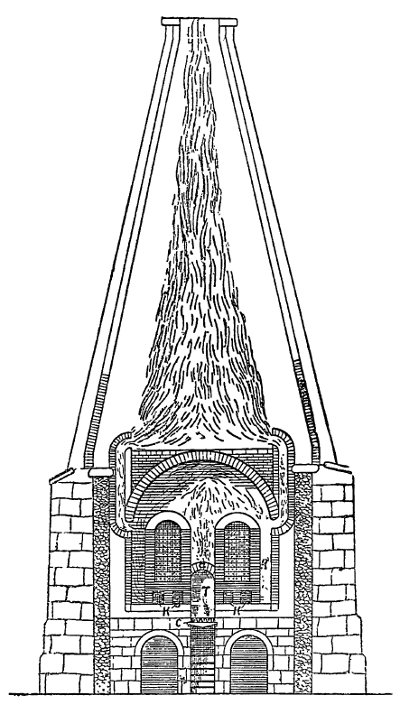
Печь для выработки цементной стали 40-х годов XIX века. Вертикальный разрез. C — колосники, они свободно лежат на поперечных балках; K — каналы, по которым проходит пламя, омывающее ящики; T — топки.
Русская техника выделки тигельной стали в сороковых, пятидесятых годах XIX века мало отличалась от современной ей английской. Командированный русским правительством для осмотра английских заводов полковник Армстронг доносил: «Описав вкратце английский способ приготовления литой стали, приятным долгом считаю присовокупить, что литая сталь мастера Бадаева, приготовляемая на Камско-Воткинском заводе из тагильского железа, на многие употребления, а именно на сверлильные бруски для сверления и обточки оружия, на зубила для рубки чугуна и прочее, не уступает литой стали английской».
Но если техника половины XVIII века достигла способов получения в практически неограниченных размерах основного сырья для черной металлургии — чугуна, если она могла добывать, правда, в малых, но вполне достаточных количествах самый высококачественный черный металл — тигельную сталь, — необходимый материал для изготовления инструментов и орудий, то сильно отстало зато среднее, если так можно выразиться, звено металлургии — выработка ковкого железа, обладающего более высокими технологическими свойствами, нежели чугун, и допускающего массовое производство. В тот год, когда Жар объезжал Англию, была сделана одна из первых удачных попыток получения ковкого железа способом, обеспечивающим до известной степени массовое его производство.
Братья Кранэдж, мастера на заводе в Кольбрукдэле, взяли патент на выработку железа из чугуна с применением каменного угля, но дальше Кольбрукдэльского завода этот способ Кранэджей — один из ранних видов так называемого пудлингования — не распространился. Английскому подрядчику Генри Корту суждено было через двадцать лет усовершенствовать, можно сказать — заново открыть этот способ.
Это была вторая победа в борьбе против недостатка топлива. Был заложен второй краеугольный камень в фундаменте, на котором построилась техника XIX столетия.
Действительно, те способы получения сварочного железа из чугуна, которые господствовали до изобретения Корта, не могли удовлетворить даже невысокий уровень техники XVIII столетия и те формы капиталистического производства, которые тогда начинали складываться. Это так называемый кричный способ, то есть переплавка чугуна в горне под сильной струей воздуха, выжигающего из металла избыток углерода и другие примеси. Необходимым условием успешности производства было применение топлива, чистого в отношении содержания серы, то есть древесного угля. Способ был долгий и кропотливый, к тому же нелегко было получить металл однородного качества, а главное — кричное производство требовало большого количества древесного угля.
Понятно, что это производство могло процветать в странах, богатых лесом, каковы были Россия и Швеция, изготовлявшие лучшие сорта сварочного кричного железа. В Швеции этот способ сохранился и до настоящего времени, но для лишенной лесов Англии он все более и более становится недоступным. Научившаяся утилизировать свои каменноугольные залежи для выплавки чугуна, страна продолжала испытывать все более и более остро железный голод, который она старалась удовлетворить все возрастающим ввозом металла из Швеции и России.
В 1716 году Англия ввезла 8 600 тонн железа, в том числе из России всего только 300 тонн, а в восьмидесятых годах XVIII века ввоз достиг 50 тысяч тонн, из которых больше половины было ввезено из России.
Корт, взявший свои знаменитые патенты в 1783 и 1784 годах, является в сущности лишь одним из последних в длинной цепи изобретателей способа переработки чугуна в железо при помощи каменного угля. К нему более чем к кому-либо другому применимо замечание Маркса: «как мало какое бы то ни было изобретение XVIII века принадлежит тому или иному лицу». При остром недостатке в древесном топливе, испытываемом в Англии уже с конца XVII века, вполне естественны были попытки заменить его каменным углем при выработке железа. Очень скоро пришлось убедиться при этом, что от переплавки чугуна с окислением его струей воздуха в непосредственном соприкосновении с каменным углем или коксом получается никуда негодное железо.
Делались попытки изолировать чугун от каменного угля, расплавляя его в закрытых тиглях вместе со шлаками, богатыми окислами железа. Способ был очень неэкономный и железо получалось невысокого качества. Надо было добиться каким-либо иным путем парализовать вредное действие горючего на металл. Средством для этого было отделение горючего от металла, сжигание его отдельно от расплавляемого металла, так, чтобы на последний могли бы воздействовать только раскаленные газообразные продукты горения.
Более чем за сто лет до Корта известна была и широко применялась в литейном деле пламенная отражательная печь. Неизвестно, когда она была изобретена, но уже колокольных дел мастера плавили в таких печах бронзу, а с конца XVII века она стала применяться и для производства чугунных отливок. Особенно широкое применение для этой цели нашли эти печи в Англии. Дело в том, что как раз каменный уголь оказывался топливом наиболее подходящим для печей этого типа. Дрова и древесный уголь давали в пламенных печах недостаточно высокую температуру для плавки чугуна. В этих «сводчатых», «купольных» печах (как их называли тогда, ибо свод, отражающий, как в то время полагали, пламя, составлял их характерную особенность) и был осуществлен этот принцип отделения горючего от перерабатываемого металла.
Пламенная печь — один из важнейших элементов кортовского способа — уже имелась налицо. То же можно сказать и про другую неотъемлемую составную часть этого технологического процесса — про прокатный стан. Уже до Корта, в XVIII веке было взято несколько патентов на прокатку железа.
Имеются смутные сведения, что уже за сто лет до Корта, в конце XVII века, выходец из Германии, некий Блауэнштейн (по-английски Блью Стон) получил ковкое железо в отражательной печи при помощи каменного угля. Мы уже говорили о братьях Кранэдж. Наконец одновременно с Кортом один литейный мастер в Южном Уэльсе, Петр Оньонс, взял патент на способ, аналогичный с кортовским: плавка в отражательной печи, перемешивание расплавленного металла, собирание его в крицы. Но Оньонс не оговаривал, что процесс ведется на каменном угле.
Изобретательность Корта заключается в широком использовании и искусном комбинировании всех результатов предшествующей техники, в новом применении уже известных элементов.
Известна печальная судьба Корта, запутанного в долговой процесс и лишившегося своих патентов, на которые жадно набросились железозаводчики, сразу почуявшие, какие огромные выгоды сулит им это новое дело.
Мы не будем останавливаться на этом. Личная судьба Корта — один из многих примеров бессовестной капиталистической эксплоатации человеческого творчества. Гораздо важнее отметить историческое значение его изобретений. Корт открыл новые возможности перед английской металлургической промышленностью. Он дал возможность перейти к массовому производству железа, той форме его производства, которая является необходимым условием капиталистического способа производства. Благодаря ему вообще могла быть осуществлена машинная и машиностроительная техника XIX века. Продукт великого изобретения Корта — пудлинговое железо, вследствие своих технологических свойств — достаточная прочность и удобство обработки — и по возможности его изготовления в достаточно больших количествах и достаточно дешево, явилось тем основным материалом, из которого строилась машина в течение почти всего XIX столетия, да и не одна машина, ведь пудлинговое железо создало железнодорожную сеть. Пудлинговое железо стало и тем материалом, из которого строились железные суда. Изобретение Корта широко открыло двери в железный XIX век.